-
随着石油工业、机械加工、食品加工与餐饮业的不断发展,含油废水的排放量日益增大。不经处理的含油废水直接排放会对周边环境造成严重的危害。含油废水中的油可分为浮油、分散油、乳化油和溶解油4种[1]。其中乳化油因其油滴尺寸较小,油水二元体系稳定性强,难以通过重力、气浮等方式实现油水分离,是最难处理的一类含油废水[2]。目前,乳化油废水处理方法包括:膜分离法、吸附法、絮凝法等[3-5]。其中的电絮凝法具有除油能力强、操作简便、自动化程度高、无需添加化学药剂等优点,是一种高效、经济、环保的含油污水处理方法[6]。电絮凝法的缺点在于废水处理过程需要消耗大量电能,导致其水处理成本相对较高。
为了降低废水处理过程的电能消耗,降低废水处理成本。近些年来提出了一种利用工作溶液盐/浓差能驱动的逆电渗析(reverse electrodialysis,RED)技术来处理各种有机/无机废水的技术[7-12]。工作溶液盐/浓差能即可来自于自然界(海水/盐湖水与入海/入盐湖的河水之间的盐差),也可以来自盐/海水分离副产物(浓盐/海水与自然盐/海水之间的盐差),还可以通过废热转换(溶液热分离)获得[13]。
1954年PATTLE[14]首次提出利用自然界盐差能的RED发电技术以来,对该技术的研究逐渐深入,各国学者发表了大量有关RED技术的研究论文。RED电堆/反应器的结构和工作原理类似。他们都是由端板、阴/阳电极,交错布置的阴/阳离子交换膜(AEM/CEM)及隔垫所构成。当浓/稀盐溶液分别流经由膜隔垫所隔两电极会产生得失电子的氧化还原反应。电子通过外部电路从阳极流向阴极,从而在外电路中产生电流。发电用的RED电堆与水处理用的RED反应器不同之处在于:电极液在RED电堆内作可逆的闭式循环,而废水作为电极液流经RED反应器电极流道并因电极的氧化还原反应生成各种反应物来降解废水中的污染物。不同的电极材料和废水成分在RED反应器电极氧化还原反应过程中会生成不同的反应物。理论上而言,若RED反应器阳极选用铁或铝作为牺牲阳极时,RED反应器可以产生电絮凝效果来处理一些难以生化降解的有机或无机废水[15]。
但实际上,因在使用过程中牺牲阳极会被不断消耗而需要定期换新,导致需要不断拆装RED反应器造成使用不便。另外,在处理含油废水过程时电极表面易被油膜污染,减弱含油废水的处理效果。为此,本课题组提出了一种如图1所示的RED电堆与常规电絮凝器耦合的乳化油废水处理系统。该系统由工作溶液的盐差能驱动RED电堆发电,电絮凝器作为负载连接在电堆的外部电路中。由于盐差能驱动的RED电堆属于内生电源。在RED电堆结构参数确定的条件下,其输出电参数(电压与电流)与外部电路负载(电絮凝器)电阻有关。而电极材料、电极间隙、处理时间、阳极钝化、含油废水参数(初始pH、电导率和温度)等变化会影响电絮凝器电阻,进而影响其工作效率。因此,本研究采用单因素法,在RED电堆结构和操作参数不变的条件下,考察电絮凝器电极材料、电极间距、支撑电解质浓度、含油废水初始pH及温度对耦合系统的乳化油废水处理效果的影响。
-
逆电渗析电堆与电絮凝器耦合系统合处理乳化油废水实验系统流程如图1所示。由图1可见,RED电堆与电絮凝器构成一串联电路。实验所用的RED电堆和电絮凝器均为自制。RED电堆由离子交换膜、丝网隔垫及电极构成,离子交换膜有40张CEM以及41张AEM(最外两侧膜采用AEM),均购自日本富士公司,型号为type 10,厚度为0.12 mm;丝网隔垫厚度为0.38 mm,孔隙率为80%;2个10 cm×10 cm×1.5 cm的钛镀钌铱板构成电极。电絮凝器由有机玻璃(透明亚克力板)制成,电解槽尺寸为20 cm×10 cm×15 cm。槽内壁设有0.3 cm宽的竖直凹槽,用来放置电极板(10 cm×10 cm×0.3 cm)。凹槽下端距电解槽底面1 cm,电极板实际有效浸没面积为90 cm2。电解槽放置在磁力搅拌器上,转子以400 r·min−1的速度不断搅拌电解槽内的含油废水,以使其保持油水均匀状态。选择这个搅拌速度值,是因为它促进了胶体和不稳定物质之间的相遇,而不会在所使用的实验装置内造成任何可察觉的聚合体破裂[16]。
-
人工配置浓度分别为0.03 mol·L−1和3 mol·L−1的稀/浓NaCl水溶液作为工作溶液并储存在相应的玻璃瓶内(5和7)。0.1 mol·L−1 的铁氰化钾水溶液作为电极液储存在避光的玻璃瓶(3)内。2台蠕动泵(6和8)泵送稀/浓溶液工作溶液流经RED电堆(11)。在稀/浓溶液盐差的作用下,浓溶液中的盐分跨膜迁移到稀溶液中,使得浓溶液浓度降低,稀溶液浓度升高。流出RED电堆的稀/浓溶液分别储存在其相应的玻璃瓶内(9和10)。一台蠕动泵(4)泵送电极液,并在RED阴/阳极回路内作循环流动,以将电荷快速转移到RED正/负极。RED电堆输出电能驱动电絮凝器工作。RED阴/阳(正/负)极与电絮凝器对应的阳/阴极用铜导线相接,构成外部电路。利用数字万用表(12和13)在线检测RED电堆输出电流和电压。RED电堆的理论开路电压可按能斯特(Nernst)方程(式(1))计算[13]。离子活度系数可用扩展的 Debye-Hückel方程(式(2))表示。
式中:U为理论开路电压,V;
为离子交换膜的选择性透过系数;Nm为膜对(membrane pair)数;z为离子价数;R为通用气体常数,8.314 J·(mol·K)−1;T为温度,K;F为法拉第常数,96 485 C·mol−1;α 为离子活度系数;C为浓度,mol·L−1。下标CEM、AEM分别代表阴、阳离子交换膜;CS和DS分别为浓和稀溶液。γ 式中:z为离子化合价;A为有效水合离子半径(
);ANa+=450pm,ACl−=300pm 为离子浓度,mol·L−1。Λ 由于流经RED电堆的浓、稀溶液浓度会发生变化,因此RED电堆理论开路电压需按浓、稀溶液平均浓度计算。本次实验固定RED电堆结构和操作参数[浓溶液浓度为3 mol·L−1,稀溶液浓度恒定为0.03 mol·L−1,过膜流速均为0.35 cm·s−1(稀/浓溶液流率均为0.134 4 L·min−1)]不变,计算得理论开路电压为6.335 V。RED电堆输出(端)电压为式(3)计算值,在RED输出电能的驱动下,电絮凝器的阳极和阴极发生的电化学反应如式(4)~式(6)所示
式中:Ri为RED电堆的内电阻,Ω,其由膜电阻,稀/浓溶液流道电阻和电极液流道及电极电阻所组成。
反应生成的单体和聚合氢氧化物作为絮凝剂具有高吸附性能,它与废水中分散的颗粒和溶解的污染物具有很强的亲和力。因此,可以通过絮凝作用去除废水中的污染物。絮凝后的产物可以通过漂浮或沉淀的方法从水相中分离出来。阴极还原反应所产生的氢气气泡可促进污染物聚结过程,有助于采用浮选去除乳化油废水中的油组份。氢气泡尺寸越小,絮凝体的截留面积越大,污染物与水的分离效果也越好[17]。此外,电场也被证明是一种有效的破乳方法。在电场力的驱动下,油滴沿着电场的方向运动,然后聚集并破乳[18]。油滴在电场中极化,导致相邻油滴之间的静电吸引力增强[19]。
-
以自制乳化油废水作为研究对象。乳化油制备过程为:每升水中含40 g15#机油(购自德国德殻石化(中国)发展有限公司)并添加8 g十二烷基苯磺酸钠作为稳定剂。采用磁力搅拌器以1 000 r·min−1的速度搅拌30 min,形成稳定的油水乳状液。去除表面浮油后的乳化油再作进一步稀释。稀释后取2 L含油量为1 g·L−1的含油废水进行实验研究。利用氢氧化钠和硫酸来调节含油废水的初始pH,并通过添加支撑电解质(Na2SO4)来调节含油废水的电导率。
实验中各种溶液配制所需的溶剂水为去离子水,所用的盐/电解质购自天津大茂化学试剂厂,为分析纯级,其所含杂质可以忽略。
实验所用的仪器有,紫外可见分光光度计(UV1780,日本岛津有限公司);蠕动泵(BT100-2J,保定兰格恒流泵有限公司);蠕动泵(KCP PRO-2-N16,卡默尔流体科技(上海)有限公司);电子天平(JJ1023BC,G电子秤有限公司);数字万用表(KEITHLEY 2110-220,美国泰克科技有限公司);低速离心机(LSC-20,上海秋佐科学有限公司);热力磁力搅拌器(EMS-9A,天津欧诺仪器股份有限公司);电导率仪(FE38,梅特勒托利多科技(中国)有限公司);pH测试仪(PXSJ-226,上海雷磁仪器有限公司)。
-
每次实验前,铁或铝阳极先要在稀硫酸溶液中浸泡15 min,捞出后用砂纸打磨再用去离子水冲洗,去除表面氧化层。在实验过程中,含油废水处理时长为60 min,每隔10 min抽取电解槽(18)中的水样。对所有水样进行离心处理,将电絮凝过程中形成的絮凝物从水相中分离出来。在每份水样中取1 mL加入氯化钠进行破乳。氯化钠投加量为总体积的5%。然后用10 mL石油醚萃取水样中的油以便测量。测量时通过紫外可见分光光度仪测试水样的吸光度,通过依据绘制的标准曲线反推其浓度。按式(7)计算除油率。为了探索操作参数变化对含油废水处理效果的影响,采用单一变量法进行实验。相同的实验重复2次。
式中:C0为含油废水中油初始质量浓度,mg·L−1;Ct为絮凝处理t时间后测得含油废水中油质量浓度(乳化后的含油废水紫外光吸收波长峰值λ=225 nm),mg·L−1。
-
电絮凝器电极选用不锈钢-铁、不锈钢-铝、石墨-铁、石墨-铝、钛镀钌铱-铁、钛镀钌铱-铝6种阴-阳极材料组合,用以考察不同阴-阳材料组合对乳化油废水去除效果的影响。图2给出了不同电极组合下极板间电压及除油率随时间的变化关系。其中,实验条件为:极板间距1 cm、含油废水中添加0.1 mol·L−1硫酸钠,pH为7.8 (pH不为7的原因是配备的乳化油中添加了支撑电解质Na2SO4,SO42-离子可以少量结合H+离子,间接引起pH升高),温度20 ℃。
由图2(a)可见,采用铝阳极时极板间电压远高于采用铁阳极,而RED的输出电压与电絮凝器采用何种阳极材料关联不大。此外,实验还发现采用铝阳极时串联电路的电流远低于采用铁阳极时的电流,因此,虽然采用铝阳极时极板间电压较高,但采用铁阳极絮凝时,RED电堆可以输出更大的电流。
根据法拉第电解定律,通过的总电荷越多,电极产生的混凝剂也越多。一方面,电流密度越大,产生的絮凝剂越多[20];另一方面,电流密度越大,阴极还原生成的氢气气泡量越大且气泡尺寸越小[21],导致气泡密度的增加,更多的小气泡也为油微粒附着于絮凝剂提供了更大的表面积,使得油水分离效率提高。
由图2(b)可见,采用铁阳极对乳化油废水的处理效果要优越于铝阳极。一方面是因为采用铁阳极可以获得较大的电流密度,有利于产生更多的絮凝剂;另一方面,铝阳极氧化过程中易形成致密的表面氧化层,导致电极电阻增大。由于表面氧化层在pH为4~10内的水溶液中非常稳定,氧化层后的铝不易被氧化成铝离子,使得铝离子与氢氧根结合生成的絮凝剂Al(OH)3量减小,絮凝效率变差。
从实验结果可以发现,采用不锈钢-铁电极组合处理含油废水的除油率最高,石墨-铁电极以及钛镀辽铱-铁电极组合处理效果次之,采用铝阳极组合电极处理含油废水的除油率最差。因此,后续均采用不锈钢-铁电极组合进行实验。
-
图3给出了不同极板间距下极板间电压及除油率随时间的变化关系。除电极间距外,其他操作参数与电极材料实验时的操作条件相同。由图3(a)可见,随着时间的延长,极板间电压均会降低。其原因在于,电解过程中电极的氧化还原反应均产生阴、阳离子且溶于废水中,会使废水的电导率逐渐增大,废水的电阻减小,极板间电压降低。由图3(a)还可见,随着极板间距的增大,电极间的电压随之增大。这是由于在相同的废水电导率下,极板间距越大,废水的电阻就越大。因此,用来克服溶液间的电阻的电压也就越大。
由图3(b)可见,当极板间距由1 cm增大至2.5 cm时,系统的除油率降低。其原因在于,絮凝器电极电阻增大,导致电流密度降低。然而,当极板间距由0.5 cm增大至1 cm时,系统的除油率反而上升。其原因在于,当絮凝器电极间距较小时,适当增大电极间距有利于改善电极间溶液的混合状态,减轻极板附近的浓差极化现象,进而有利于金属离子的溶出,形成絮凝体。
由于需要处理的乳化油废水电导率较低,采用较小的极板间距可以降低用于克服溶液电阻所损失的电压。但极板间距过小时,电极氧化还原反应过程的浓差极化现象较为严重。通过实验发现,对于所研究的RED-EC耦合废水处理系统,采用1 cm的极板间距较为合适。因此,后续实验中极板间距均为1 cm。
-
支撑电解质浓度变化会影响废水电导率变化,进而会影响电絮凝器电极间废水电阻值,从而影响RED电堆的输出电流和系统的除油率。为了考察支撑电解质浓度变化对除油率的影响,在模拟乳化油废水中添加不同浓度的硫酸钠。图4给出了不同支撑电解质浓度下,极板间电压及除油率随时间的变化关系(除废水中支撑电解质浓度外,其他操作参数与电极材料实验时的操作参数条件相同)。
比较图4(a)和图4(b)可见,当模拟乳化油废水中不添加支撑电解质(硫酸钠浓度为0 mol·L−1)时,极板电压很高,RED电堆的输出电流很小,除油率较低,仅为36.7%。其原因在于,配制的不含支撑电解质的模拟乳化油废水的电导率很低,溶液电阻很大,导致极板间废水所损失的电压很大,RED电堆输出电流减小,除油率降低。当向模拟乳化油废水加入少量支撑电解质(硫酸钠浓度为0.05 mol·L−1)后,废水的电导率会迅速增加,废水的电阻迅速降低,电极电压也随之降低,RED电堆的输出电流随之增加,除油率也随之增大。如果继续增加废水中的支撑电解质浓度,尽管废水电导率会增大,但增大的幅度逐渐变小,对电絮凝器电极电压的影响也会逐渐降低,除油率增速逐渐减小。因此,在采用电絮凝法处理含油废水时,可根据废水的实际电导率来添加支撑电解质量。
-
由于含油废水初始pH会影响影响金属氢氧化物(絮凝剂)的形成。因此,该值变化对电絮凝过程会产生较大的影响[22]。为了探索不同初始pH对实验系统除油率的影响,在其它操作参数不变的情况下,通过添加氢氧化钠或硫酸调节废水初始pH(初始pH为3~11),考察初始pH对RED-EC耦合废水处理系统的除油率的影响关系。
图5给出了在不同初始pH条件下,含油废水pH随处理时间的变化情况。由图5可见,当含油废水初始pH较低时,随着处理时间的增加,废水的pH也会随之增加。其原因是由于在电絮凝过程中阴极还原反应产生了氢氧根(OH−)((5))。但随着含油废水初始pH的增大,随着处理时间而变化的废水pH增速逐渐减小。当初始pH为11时,废水的pH不再随处理时间的变化而变化,几乎保持恒定。
图6给出了不同初始pH条件下,极板间电压及除油率随时间的变化关系。由图6(a)可见,当初始pH偏离7(中性)越多,电极电压相对越低,相应的RED电堆输出电流也就相对越大。其原因在于,添加的酸或碱都属于强电解质,其浓度越高废水的电导率越大,极板间溶液电阻越小,极板间电压越小。当废水初始pH为3时,极板间电压随着处理时间的延长而增大。其原因在于,电絮凝反应产生的部分OH−与酸中的H+中和成水,废水的pH升高(图5),电导率降低所致。而当废水初始pH为中性或弱碱性时,极板间电压随着处理时间的延长而减小,原因在上述分析中已有阐述。
由图6(b)可见,当废水初始pH为中性时,耦合系统的除油率最高。而初始pH太低或太高均对耦合系统的除油率不利。影响耦合系统电絮凝除油效果是多方面的。从预防电极钝化的思路考虑,当pH较低时,电极氧化膜易于溶解,使得电极钝化现象得到延缓。而从絮凝的角度看,中性偏碱性条件更有利于Fe(OH)3絮体形成,以达到较好的絮凝效果[23]。正是由于这两种相互矛盾关系的影响,初始pH在5~9内含油废水经耦合系统处理60 min后的除油率可达到80%以上。
-
电絮凝处理含油废水时,废水温度变化会对除油率产生影响。在电极为不锈钢-铁电极、极板间距1 cm、支撑电解质浓度0.1 mol·L−1、pH为7.8的条件下,不同温度下极板间电压及除油率随时间的变化情况如图7所示。由图7(a)可见,随着电解槽内的含油废水温度升高,电极板间的工作电压降低,RED电堆输出电流增加。其原因在于,随着废水温度的升高,溶解于废水中的金属盐溶质“颗粒”的布朗运动强度增加,溶液电导率增大,电极板间的溶液电阻减小,使得电极电压降低。PAZENKO等[24]研究了废水温度对电絮凝法处理含油废水的影响,得出温度越高,电导率越高,能耗越低的结论。由图7(b)可见,在相同的处理时间内,耦合系统对含油废水的除油率随温度的升高而增加,验证了PAZENKO文献[24]得出的结论。因此,在有条件时,适当提高含油废水温度有利于提高耦合系统处理效率。
-
1)与采用铝阳极材料相比,采用铁阳极材料的耦合废水处理系统具有更高的除油率。
2)极板间距和含油废水参数(电导率、初始pH和温度)变化会对耦合废水处理系统的除油率产生影响。过大或过小的极板间距均对系统的除油率不利,在所研究的系统中,电絮凝器极板间距为1 cm时最佳;当废水的电导率很低时,系统的除油率很小,适当增加废水的电导率可以迅速提高系统的除油率;中性或微碱性条件下系统的除油率较高;温度越高,系统的除油率也越高。
3)采用不锈钢-铁电极,1 cm电极间距,0.1 mol·L−1支撑电解质(Na2SO4)浓度,pH 7.8和40 ℃的实验条件下,经耦合废水处理系统处理60分钟后的含油废水除油率可达到98.39%。
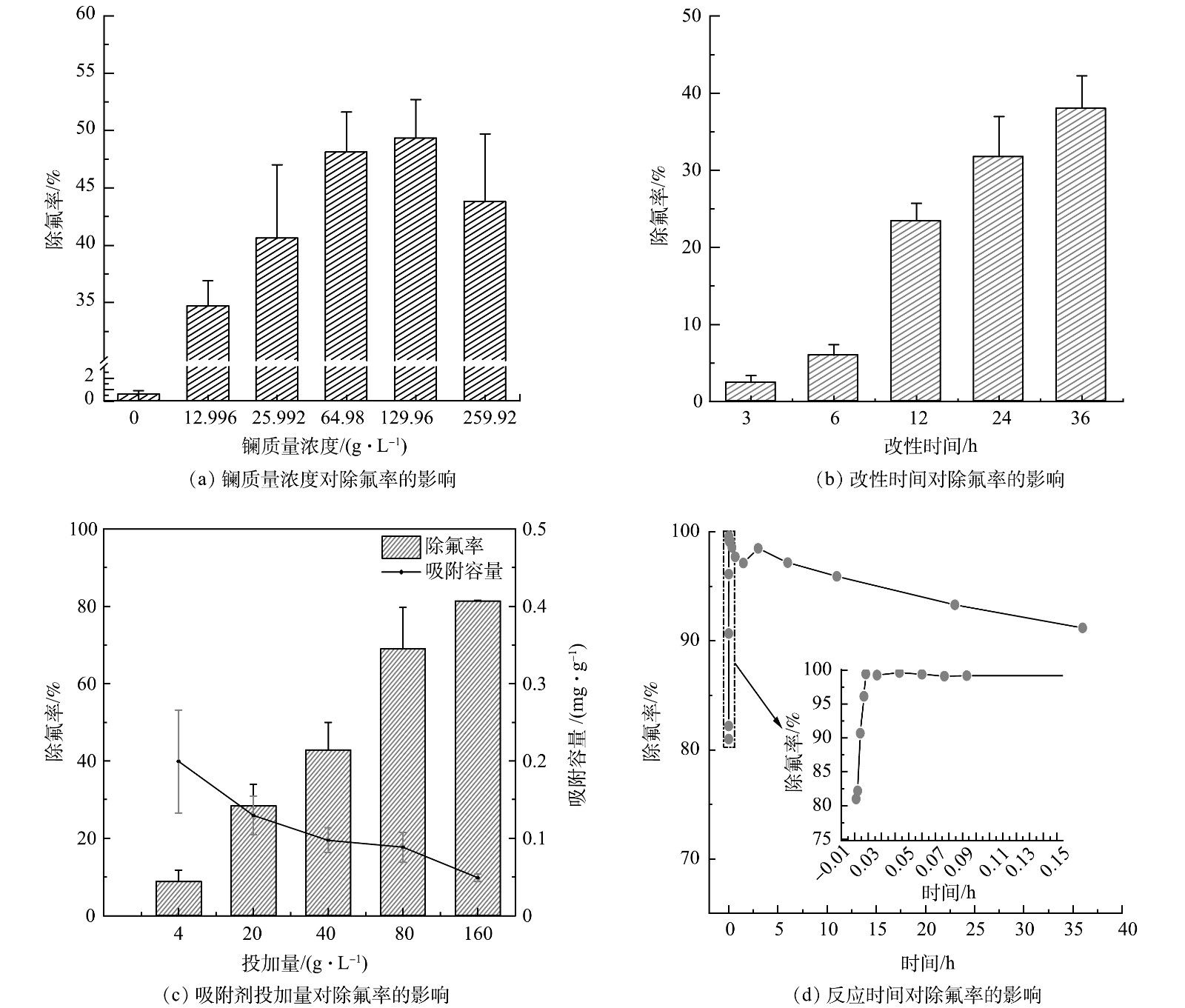