-
化学合成工业的蓬勃发展,在给人类生活带来便捷、高效、舒适生活的同时,亦给生态环境保护和人类健康带来巨大安全隐患。其中,废水中的酚类污染物主要来源于焦化厂、煤气发生站、合成酚厂、制药厂、合成纤维厂等化工生产过程产生的含酚废水[1],酚类化合物在生物体内能够使细胞组织失去活性[2],由于其高毒性、难降解、易生物积累等特性而受到广泛关注[3],苯酚、间甲酚、2,4-二氯酚、对硝基苯酚等6种酚类被列为我国水体优先控制污染物黑名单。如何去除与回收工业废水中的酚类化合物是目前国内外化工与环境领域关注的焦点问题之一。
目前,水体中酚类化合物的常用去除方法主要有萃取法[4]、吸附法[5-6]、生物降解法[7-8]及高级氧化法[9-10]等。溶剂萃取法工艺简单、易操作,但仅用于对高浓度含酚废水进行预处理;吸附法脱酚效率不高,需与其他脱酚方法联用;生物降解法经济可靠,但一般用来处理较低浓度的含酚废水;高级氧化法处理效果好,但成本高,目前工业上应用较少。乳化液膜法在20世纪70年代初期提出,能实现对液相中酚的分离与富集[11],具有低能耗、低成本、界面面积大、传质速率高、操作简单等特点,受到国内外研究者的广泛关注[12-13]。
传统乳化液膜多采用石油基溶剂,如煤油[14-15]、环乙烷[16]、正庚烷[17]等,具有毒性且不可被生物降解、不能再生,如果排放到环境中将对环境产生巨大危害[18]。采用绿色可持续的植物油来代替传统石油基溶剂是目前的一大研究趋势。棕榈油已被报道作为乳化液膜的绿色稀释剂用于分离苯酚(83%)[19]、银(97%)[20]、活性染料(90%)[18]、铬(97%)[21]等,其中分离苯酚的效果并不理想。本研究采用棕榈油作为绿色稀释剂来制备乳化液膜用于去除和回收焦化废水中的苯酚,以聚异丁烯多丁二酰亚胺(T-155)作为表面活性剂同时配以载体正辛醇,以期提高GELM体系分离酚的能力。本研究以模拟含酚废水为研究对象,通过单因素实验研究油内比、表面活性剂浓度、载体浓度、内水相浓度、制乳时间及制乳转速对乳化液膜稳定性的影响,考察表面活性剂浓度、载体浓度、内水相浓度、油内比、乳外比、搅拌转速和萃取时间苯酚去除率的影响,并研究该乳化液膜对不同酚类的去除效果和对苯酚的富集能力,以期为实验室研究与工业化应用提供参考。
-
试剂:工业煤油、氢氧化钠、正辛醇、铁氰化钾、氯化铵、氨水、4-氨基安替比林、苯酚均为分析纯;T-155、棕榈油为工业级;仪器:722光栅分光光度计、JJ-1A160W数显电动搅拌器(金坛新瑞)、JRJ300-SH型剪切乳化搅拌机(上海沪析)。
-
取一定量的乳化液置于玻璃毛细管内,放置24 h,观察破乳情况,记录破乳量,破乳率按式(1)计算。用乳化液膜分离提取模拟废水中的苯酚,苯酚去除率按式(2)计算,提取前后苯酚富集倍数按式(3)计算。
式中:Vt为放置24 h后乳化液的破乳量,mL;V0为放入毛细管中的乳化液的体积,mL;Ƞ为破乳率,%;
为模拟废水苯酚初始浓度,mg·L−1;$ {\rho }_{0} $ 为萃取水相的苯酚浓度,mg·L−1;$ {\rho }_{\mathrm{A}} $ 为破乳后水相中的苯酚浓度,mg·L−1;n为脱酚率,%;m为苯酚富集倍数。$ {\rho }_{\mathrm{E}} $ 采用4-氨基安替比林分光光度法(HJ 503-2009)测定废水中苯酚的含量、重铬酸钾法(HJ 828-2017)测定废水的COD。
-
将苯酚与去离子水混合配制成一定浓度的模拟废水,以模拟废水为研究对象,研究制备的乳化液膜对酚的去除能力。有研究指出[22],棕榈油和煤油按7∶3的比例混合得到的乳液最稳定,因此本研究中棕榈油与煤油的比例确定为7∶3。先将棕榈油和煤油按比例混合,然后将表面活性剂溶解于棕榈油和煤油的混合物中,用电动搅拌器对混合物进行搅拌,并加入载体。待搅拌均匀后,加入一定浓度的NaOH溶液作为内相,如图1所示,将搅拌好的液体立即用剪切乳化搅拌机制乳[23],即可制得油包水型(W/O)乳白色油状液膜。按照一定的乳外比(乳液与外相溶液的体积比),将一定量的乳化液加入到含酚废水中,并用电动搅拌器使混合液搅拌均匀。W/O型乳化液分散至外相中形成水包油再包水型(W/O/W)乳化液膜体系。待传质过程结束后,停止搅拌,让混合液静置分层,然后取出50 mL下层清液,用于测定酚含量。同时收集分层后的乳液,通过加热破乳使乳化液与内水相分离,浓缩回收内水相中的苯酚。
-
以棕榈油和煤油的混合物为膜溶剂,体积分数为4%的T-155为表面活性剂,体积分数为0.4%的正辛醇为载体,内相浓度为0.1 mol·L−1,制乳转速为1 300 r·min−1,制乳时间5 min,研究不同油内比对乳化液膜稳定性的影响,结果如图2(a)所示。油内比增大时乳化液的破乳率会下降。油内比较低时有机溶剂不足以实现对内相溶液的适当包封,从而使得液膜较薄,乳液不稳定[24]。油内比增大会使得液膜变厚,稳定性提高。但油内比过大会导致液膜的黏度、厚度增大,使待分离物质在膜内的传质速率下降,所以应该在保证稳定性较好的前提下选择较小的油内比。本实验确定油内比为1∶1。在研究表面活性剂浓度、内相浓度、油内比、制乳转速以及制乳时间相同的实验条件下,研究不同载体浓度对乳化液膜稳定性的影响,结果如图2(b)所示。破乳率随着载体浓度的增加会先增大后减小,在载体浓度为0.4%时破乳率最低。AHMAD等[25]指出,过多的载体会使更多的溶质从外相快速转移到内相,导致外相和内相之间渗透梯度的显著变化,从而使得乳化液滴膨胀、液膜破裂。本实验选用载体正辛醇的浓度为0.4%。
以棕榈油和煤油的混合物为膜溶剂,0.4%的正辛醇为载体,油内比为1∶1,内相浓度为0.1 mol·L−1,制乳转速为1 300 r·min−1,制乳时间5 min,研究不同表面活性剂浓度对乳化液膜稳定性的影响,结果如图2(c)所示。可见,破乳率随着表面活性剂的增加会先升高后降低,在表面活性剂浓度为4%时破乳率最低。增加表面活性剂的浓度可以降低表面张力,从而形成更多的细小液滴,产生更稳定的乳液[26]。但随着表面活性剂用量增加到一定量时,会降低了乳化液滴的运动速率,导致液滴发生溶胀[27]。本实验选用表面活性剂T-155的浓度为4%。在研究表面活性剂浓度、载体浓度、油内比、制乳转速以及制乳时间相同的实验条件下,研究不同内相浓度对乳化液膜稳定性的影响,结果如图2(d)所示。当内相浓度为0.1 mol·L−1时,破乳率最低,在内相浓度大于0.1 mol·L−1后,随着浓度的增大,液膜的稳定性变差。KUMAR等[28]指出,在较高内相氢氧化钠浓度下,氢氧化钠会与表面活性剂发生反应,使表面活性剂水解,从而导致乳化液膜的稳定性降低。本实验选用内相浓度为0.1 mol·L−1。
以棕榈油和煤油的混合物为膜溶剂,4%的T-155为表面活性剂,0.4%的正辛醇为载体,油内比为1∶1,内相浓度为0.1 mol·L−1,制乳转速为1 300 r·min−1,研究不同制乳时间对乳化液膜稳定性的影响,结果如图2(e)所示。可见,制乳时间越长,乳化液的破乳率越低,制乳时间大于5 min后,破乳率变化不大。制乳时间越长,液膜粒径就越小,粒径分布范围也就越小,分散效果越好,反之分散效果会降低,导致乳化液膜的稳定性受到影响[29]。并且过长的乳化时间会使得内相液滴一直在高速剪切下,导致进入内相的水的转移速率增加,从而造成膜破损[30]。本实验选用制乳时间为5 min。在研究表面活性剂浓度、载体浓度、油内比、内相浓度以及制乳时间相同的实验条件下,研究不同制乳转速对乳化液膜稳定性的影响,结果如图2(f)所示。制乳转速为1 300 r·min−1时,破乳率最低。油相在剪切力的作用下分散为均匀的乳化液颗粒,当剪切力过大时会破坏乳化液颗粒,使得乳滴半径太小而会快速结合,当膜无法克服碰撞力时便导致乳液液滴破裂[19]。本实验选用制乳转速为1 300 r·min−1。
-
以棕榈油和煤油的混合物为膜溶剂,4%的T-155为表面活性剂,0.4%的正辛醇为载体,内相浓度为0.1 mol·L−1,乳外比为1:3,搅拌转速500 r·min−1,萃取时间5 min,研究不同油内比对100 mg·L−1的模拟苯酚废水去除率的影响,结果如图3(a)所示。油内比是制备乳化液膜时添加的油相与内相的体积比。随着油内比的增加,脱酚率会先升高后降低,当油内比为1:1时脱酚率最高。从经济角度来看,降低油内比可以减少制备乳化液膜原料的使用量,从而提高经济效益;从处理效果方面来看,提高油内比可以形成更稳定的乳液,但油内比过大会使得液膜厚度增加,导致待分离物质在膜内的传质速率下降[31],脱酚率下降。本实验选择油内比为1∶1。在研究表面活性剂浓度、内相浓度、油内比、乳外比、搅拌转速以及萃取时间相同的实验条件下,研究不同载体浓度对100 mg·L−1的模拟苯酚废水去除率的影响,结果如图3(b)所示。随着载体浓度的增加,脱酚率先增加而后基本保持不变。载体正辛醇是直链氢键缔合溶剂,能与酚形成弱氢键缔合物[32],可实现对苯酚的选择性迁移,使得传质效率增大。由于棕榈油中的主要成分甘油三酯可以与苯酚形成苯酚-甘油三酯络合物,故棕榈油的存在有利于Ⅱ型传质,可促进苯酚迁移至膜内,而外加载体有利于脱酚率的进一步提高。当外加载体正辛醇的浓度增加到0.4%时,脱酚率达到最大值,说明此时载体浓度最佳。当载体浓度继续增加时,载体会有富余,经济效益下降,同时载体过多会使得乳液粘度变大而增加传质阻力[33],导致脱酚率降低。因此,本实验选择载体浓度为0.4%。
以棕榈油和煤油的混合物为膜溶剂,4%的T-155为表面活性剂,0.4%的正辛醇为载体,内相浓度为0.1 mol·L−1,油内比为1∶1,乳外比为1∶3,萃取时间5 min,研究不同的搅拌转速对100 mg·L−1的模拟苯酚废水去除率的影响,结果如图3(c)所示。当转速为500 r·min−1时脱酚率最高。搅拌速度越高,强化了乳化液膜的传质过程,同时会产生较大表面积的细小液滴,可促进苯酚转移至膜内[34]。反之,当转速过低时,乳液不易分散完全,导致传质效果不好,脱酚率低。但在过高的搅拌速度下,形成的乳液液滴尺寸小,液膜变薄,乳液液滴会迅速聚结,最终导致膜破裂,脱酚率下降。因此,本实验选择的转速为500 r·min−1。在研究表面活性剂浓度、载体浓度、油内比、乳外比、搅拌转速以及萃取时间相同的实验条件下,研究不同内相浓度对100 mg·L−1的模拟苯酚废水去除率的影响,结果如图3(d)所示。随着内相浓度的增加,当内相浓度小于0.5 mol·L−1时,脱酚率会有所增加,而当内相浓度超过0.5 mol·L−1时,脱酚率不随内相浓度的增大而增加。内相浓度越高,传质推动力增大,脱酚率变大。但NaOH浓度过高会使得乳化液膜的稳定性下降,同时高浓度的内相试剂会在外相和内相之间产生显着的渗透压差,导致乳液液滴尺寸增加,液滴更易破裂[35],ROUHANI等[36]研究也表明,内相试剂浓度过大时会降低液膜厚度,从而导致脱酚率下降。从乳化液稳定性和脱酚率的角度来看,当NaOH浓度为0.2 mol·L−1时液膜破乳率较低,脱酚率也较高,因此,本实验选择内相浓度为0.2 mol·L−1。
以棕榈油和煤油的混合物为膜溶剂,0.4%的正辛醇为载体,内相浓度0.2 mol·L−1,油内比为1∶1,乳外比为1∶3,搅拌转速500 r·min−1,萃取时间5 min,研究不同载体浓度对100 mg·L−1的模拟苯酚废水去除率的影响,结果如图3(e)所示。当表面活性剂浓度为4%时,脱酚率最大。表面活性剂的加入可以降低界面张力,有助于小粒径的乳液液滴的形成,从而增大外相与乳化液膜之间的接触表面积[37],有利于酚的迁移,但当表面活性剂增大到一定量之后会导致液膜厚度增加、界面粘度变大从而使得传质阻力增大[38],脱酚率降低。因此,本实验选择表面活性剂浓度为4%。在研究表面活性剂浓度、载体浓度、内相浓度、油内比、搅拌转速以及萃取时间相同的实验条件下,研究不同乳外比对100 mg·L−1的模拟苯酚废水去除率的影响,结果如图3(f)所示。随着乳外比的增大,脱酚率也相应增大。HUSSEIN等[39]发现较低的乳外比会使得外相和乳液之间的渗透压差增加,从而导致液膜更易破裂,脱酚率下降。而对于一定体积的外水相而言,乳外比越大,用来萃取的乳液量就越大,乳液与外水相的接触面积越大,使得脱酚率提高,但消耗的乳液多,经济效益下降。实际应用中需用较小的乳外比达到所要求的条件。本实验选择乳外比为1∶3。
以棕榈油和煤油的混合物为膜溶剂,4%的T-155为表面活性剂,0.4%的正辛醇为载体,内相浓度0.2 mol·L−1,油内比为1∶1,乳外比为1∶3,搅拌转速500 r·min−1,研究不同的萃取时间对100 mg·L−1的模拟苯酚废水去除率的影响,结果如图4(a)所示。随着萃取时间的增大,脱酚率先升高后降低,当萃取时间为5 min时,脱酚率最大。萃取时间的增加有助于将大的乳液液滴破碎成大量较小的乳液液滴,从而增大传质表面积[40],使得酚与液膜接触越充分,提高脱酚率。但随着萃取时间的延长,由于更多的外相分子转移到内相中,会使乳液溶胀,最终导致膜破裂增加[28],脱酚率下降。因此,本实验选择萃取时间为5 min。在研究表面活性剂浓度、载体浓度、内相浓度、油内比、乳外比以及搅拌转速相同的实验条件下,研究萃取时间对100 mg·L−1的不同酚类模拟废水COD去除率的影响,结果如图4(b)所示。随着萃取时间的增大COD去除率先增大后减小,这与萃取时间对脱酚率的影响规律一致,当萃取时间为5 min时,COD去除率最大,达到73.71%。
以棕榈油和煤油的混合物为膜溶剂,4%的T-155为表面活性剂,0.4%的正辛醇为载体,内相浓度0.2 mol·L−1,油内比为1∶1,乳外比1∶3,搅拌转速500 r·min−1,萃取时间5 min,研究该乳化液膜体系对不同浓度的模拟苯酚废水去除率的影响,结果如图5所示。在初始苯酚质量浓度小于1 000 mg·L−1的情况下,苯酚浓度的变化对脱酚率的影响不大,在初始苯酚质量浓度达到300 mg·L−1时脱酚率最高,达到99.53%。当初始苯酚质量浓度大于1 000 mg·L−1时,随着苯酚浓度的增大,脱酚率有所下降,但在初始苯酚浓度为4 000 mg·L−1时,脱酚率仍达90.51%,说明该乳化液膜体系在处理高浓度含酚废水方面具有一定优势。苯酚浓度的提高可以增加传质推动力,从而使得脱酚率增大,但当苯酚浓度提高到一定值后,由于液膜中NaOH的量一定,液膜能脱除的酚有限,从而使得脱酚率下降。
以棕榈油和煤油的混合物为膜溶剂,4%的T-155为表面活性剂,0.4%的正辛醇为载体,内相浓度0.2 mol·L−1,油内比为1∶1,乳外比1∶3,搅拌转速500 r·min−1,萃取时间5 min,研究该乳化液膜体系对不同酚类模拟废水去除率的影响,结果如图6所示。该乳化液膜体系对于邻甲酚、邻氯苯酚和邻氨基苯酚这3种酚类去除率均较高,去除率均接近99%,说明该乳化液膜体系对于与苯酚化学性质相似的酚类的脱除效果较好。
-
本实验进行了通过加热破乳来回收乳化液膜中的酚研究。在70 ℃的恒温水浴锅中,将液膜提取分离后的乳状液(乳液相)加热120 min,即可实现破乳。将破乳后的水相分离出来,测定水相中的酚浓度,计算苯酚富集倍数。对于相同的乳化液膜,改变乳外比,分析其对苯酚富集倍数的影响,结果如图7中所示。由图7以看出,随着乳外比的增加,苯酚富集倍数增大,从1∶3处理比的5.73倍到1∶10处理比的16.47倍富集。
-
1)当表面活性剂T-155浓度为4%、载体正辛醇浓度为0.4%、内相试剂NaOH溶液浓度为0.1 mol·L−1、油内比1∶1、在1 300 r·min−1的转速下进行5 min高速剪切制乳是制备乳化液膜的最佳条件。
2)当表面活性剂T-155浓度为4%、载体正辛醇浓度为0.4%、内相试剂NaOH溶液浓度为0.2 mol·L−1、油内比1∶1、乳外比为1∶3,在500 r·min−1的转速下萃取5 min除酚率可达99.45%,COD去除率可达73.71%,并且该乳化液膜体系对于邻甲酚、邻氯苯酚和邻氨基苯酚这3种酚类去除率均接近99%,当初始酚质量浓度达到4 000 mg·L−1时,脱酚率仍然接近90%。
3)该乳化液膜对苯酚的富集倍数随乳外比的增大而增大,在乳外比为1∶10时富集倍数可达16.47。
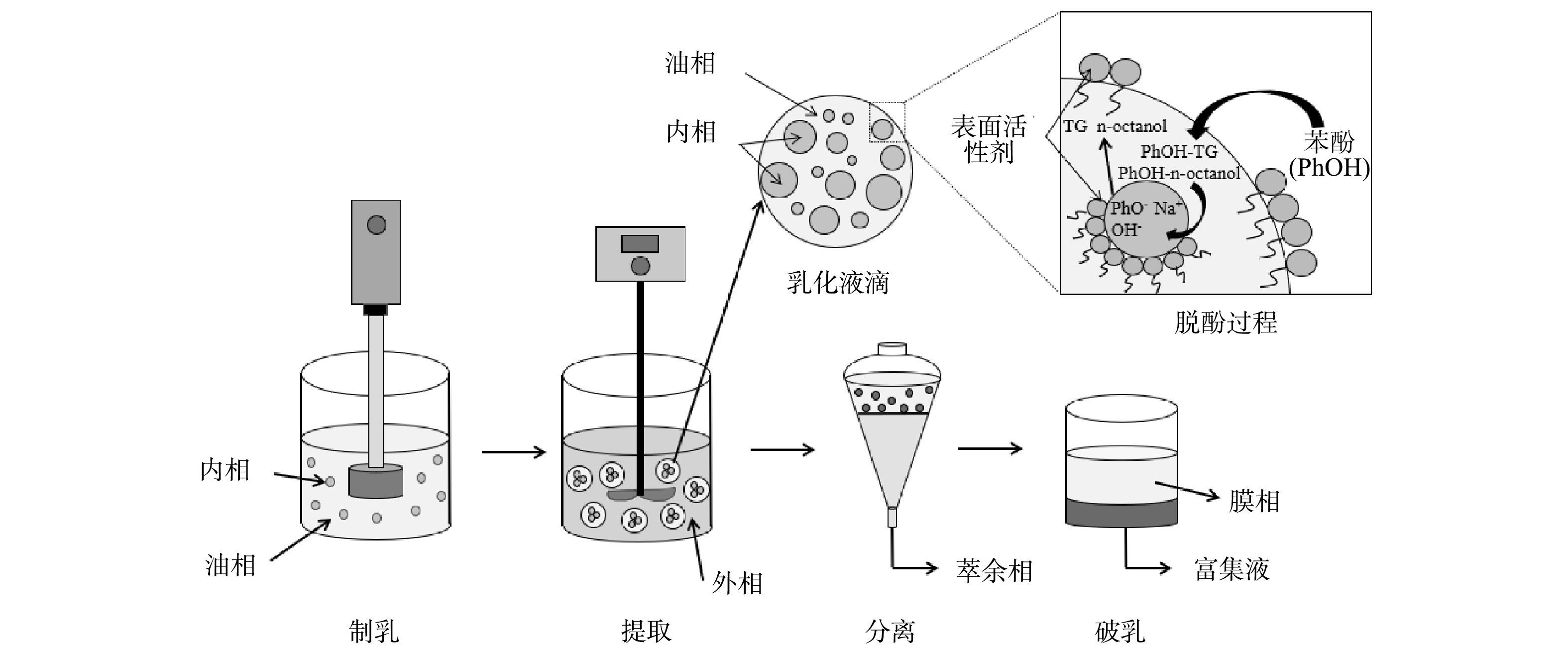