-
挥发性有机化合物 (volatile organic compounds,VOCs) 是指常温下,沸点在50~260 ℃范围内的有机物[1]。目前,我国工业源VOCs的排放量约占人为源VOCs排放量的50%左右[2-3],主要来源于石油炼化、合成材料、涂料、制药、橡胶、印刷、漆包线生产等行业[4-7]。近年来,随着制药行业的快速发展,需要在生产过程中大量使用挥发性有机溶剂,在反应体系溶解、分离提纯等过程中会产生大量VOCs[8]。工业排放的VOCs主要呈现种类多、流量大,且呈不连续、不稳定等特点[9-15]。
制药行业排放的VOCs治理方法包括燃烧净化法、吸收法、吸附法、冷凝法、生物法、光催化氧化法、等离子体净化法等[16-22]。针对制药行业VOCs排放呈流量大和间歇性特点,很难利用传统方法实现对VOCs质量浓度为22~6 293 mg·m−3波动条件下的连续处理,并使其达到排放要求。这是由于燃烧净化法需保持恒定炉内温度,才能实现对炉内有机废气的持续燃烧净化;而在炉内废气质量浓度小于800 mg·m−3时,则会停止工作,造成燃烧间断。一种处理间歇性VOCs的方法是在进气口增加浓度监测设备,当浓度较低时对进气口的冷气进行预热,但该方法存在延时问题,预热设备频繁启动也会增加能耗[23]。此外,燃烧过程需通过控制可燃物浓度来实现对温度的精准控制,但催化燃烧过程很难用线性化模型表示[24-25]。因此,针对制药行业大流量、间歇性有机废气的排放处理问题上,仍存在很多难点。
陈飞等[26]通过对蓄热+换热的传统催化燃烧装备进行废气换热器、电加热棒、处理器上盖板、气流隔板、废气进口管、出口管等的改造,实现了VOCs废气净化装备连续运作,且效率更高。张跃斌等[27]针对催化燃烧的废气采用电加热方式,采用PLC系统依温度条件精密控制,当废气温度低于设定温度下限时电热管会自动给废气加热,当废气温度高于设定温度上限时电热管会按照设定条件自动断开,并依次进行第一组加热、第二组加热,直至断开全部电源以节约电能、实现节能运行。当脱附气体中的废气浓度达到一定浓度后,基本可实现热量的自动平衡,无需开启电加热,可节约用电,是一种适合低温 (约350 ℃) 废气催化燃烧的新工艺。YU等[28]设计了一种催化热交换器,采用燃烧空气的蓄热预热系统。该催化换热器由催化燃烧室和热交换器组成。该研究考察了空气-燃料混合气的当量比、速度、预热温等操作参数的敏感性,为催化换热器中找到稳定催化燃烧的最佳操作条件。FENG等[29]针对微催化多孔燃烧室丙烷催化燃烧过程,建立了耦合晶格玻尔兹曼模型,揭示了微催化多孔燃烧室的燃烧机理和影响转化效率的主要因素取决于当量、燃气温度和支撑材料的性质。
本研究以催化燃烧法为基础,构建由蓄热、换热、回热和补热组成的多效热回收工艺,结合模糊比例积分微分 (proportion integration differentiation, PID) 温度控制策略,以镀在蜂窝陶瓷载体上的铂钯合金为催化剂,对VOCs进行多效热回收的直接催化燃烧,进一步将此方法应用于北京某制药厂,对该厂存在的大流量、间歇性有机废气进行处理,验证工艺可行性,以期为制药行业或其他行业的VOCs治理提供参考。
-
多效热回收的催化燃烧装置由蓄热、换热、回热和补热4个部分组成。蓄热部分由1层陶瓷蓄热砖和5层厚度为40 mm蜂窝催化层组成,放置在催化燃烧炉中间位置;换热部分由十字交叉的金属薄板组成,交换燃烧前后气体温度;回热部分则通过建立炉外循环,通过循环风机将一部分燃烧废气送回燃烧炉,形成对燃烧热量的回收;最后,在炉外循环路径上增加酒精燃烧机,通过调节回热风机功率,稳定循环内的温度,从而实现补热效果。由于该制药厂主要使用的溶剂为酒精,其来源方便,且废酒精较多,加上该药厂无天然气管道,故采用酒精燃烧机补热。
催化燃烧炉直径为1.8 m,高度为3.8 m,材质为碳钢,催化剂床的进气口为收缩结构,直径为3 m,共用4个进气口,通过增大局部气体流速的方式实现多室动力平衡,平均催化床温度。催化剂采用500 g·m−3铂钯合金,设计空速10 000 h−1,填充在体积为2 m3的蜂窝催化床上,可实现对通气量为20 000 m3·h−1的稳定催化燃烧。换热器尺寸 (长×宽×高) 为1.2 m×1.2 m×1.6 m,由0.1 mm金属薄板组成,相邻换热管的间距≤10 mm。循环内的加热装置由电加热器和酒精燃烧机2部分组成。其中,电加热装置尺寸 (长×宽×高) 为1.78 m×0.68 m×1.1 m,仅在启炉过程使用,通过调节燃烧机的酒精流量阀,控制酒精补充量,间接调节炉内温度。
系统由三元流风机(5.5 kW)提供循环内的VOCs气体压力,装置设计的最大温度为570 ℃,升温速度≤3 ℃ min−1,排气压力3 kPa、额定VOCs流速≥4.5 m·s−1。
催化炉前端采用干式过滤器尺寸 (长×宽×高) 为2.25 m×2.25 m×4 m,为碳钢材质,采用不锈钢丝网+F5级布袋过滤。催化炉后端采用喷淋工艺对废气进行降温并进一步降低废气浓度。采用三级喷淋,每个喷淋塔为Φ 1.5 m×4.5 m,塔内停留时间为3 s,气液比为3‰,气速为3 m·s−1。配套2.2 kW的水泵,流量为15 m3·h−1,扬程17 m。主风机采用玻璃钢材质,功率30 kW,风量为20 000 m3·h−1,压力为3 000 Pa。
-
系统的工艺流程图如图1所示。首先,增压风机提供负压,抽取车间中的废气,通过过滤器进行过滤 (F5级过滤) ,去除废气中的细微粉尘和杂质等颗粒物;第二,过滤后的废气经过换热器后,吸收准备排出的气体热量,实现第1次升温;第三,废气进入催化燃烧炉,VOCs经过镀有铂钯合金的蜂窝蓄热催化床,实现直接催化燃烧;第四,经过催化燃烧炉的一部分气体进入热量补充循环,经过由酒精燃烧机和电加热装置组成的补热器,通过回热风机的增压作用,再次进入催化燃烧炉;第五,另一部分气体经过换热器降温和喷淋塔冷却排入大气。
补热器由电加热器和酒精燃烧机组成,电加热器仅在启炉过程中使用。控制器通过控制酒精燃烧机中酒精的摄入量,控制系统回路中的酒精浓度,稳定催化燃烧炉内的温度。VOCs净化现场照片如图2所示。
-
本装置中的被控对象 (即催化燃烧炉内温度) 为回热循环中的酒精浓度。催化燃烧过程很难用线性模型表示,多效热回收工艺的组成形式增加了控制系统的非线性度,该系统的PID参数不能通过线性化方法得到。为提升工程的可靠性,装置采用基于模糊PID温度控制策略,通过控制调节回热风机功率,调节经过酒精燃烧机的气体流量,将催化燃烧炉的炉温稳定在300~400 ℃,以实现炉内燃气稳定燃烧。模糊PID控制利用模糊逻辑并根据模糊规则对PID的参数进行实时优化,能克服传统PID参数无法实时调整PID参数的缺点[30]。由于燃烧系统受到多种因素影响,难以建立准确的模型系统,使用模糊PID控制能有效提高PID控制算法的效果,提高系统稳定性及控制系统的准确度[31-33]。
系统首先利用西门子热电偶采集模块EM AT04和K型热电偶搭建一个多通道温度数据采集平台;其次,基于西门子200SMART PLC设计软件及触摸屏操控界面组成稳定可靠的控制系统;最后根据多效热回收的催化燃烧技术工艺流程和燃烧炉内的温度变化规律,利用基于燃烧过程的模糊理论,对PID控制逻辑中的控制参数进行实时优化,构建基于温度偏差量
的PID参数调节方法。本工艺采用基于模糊PID控制方法的控制逻辑 (图3)。ΔT 系统中的温度传感器会实时采集燃烧炉内的温度,控制系统经过计算,得到当前值与设定值的偏差 (
) 及偏差量的变化量 (ΔT ) 2个值,使用模糊理论建立比例因子eΔT 、积分因子Kp 、微分因子Ki 与系统偏差Kd 与偏差变化率ΔT 间的关系,计算方法如式(1)~式(3)所示。eΔT 在具体实现的过程中,当系统出现偏差时,将偏差与偏差变化率转化为模糊变量,通过建立的模糊规则,修正PID控制器的3个参数。系统对修正后的比例、积分、微分进行控制,直到无偏差。本装置最终修正的比例系数、积分系数和微分系数分别为P=0.5、I=0.95、D=0.08。
-
(1) 废气采集方法。制药厂废气使用智能双烟路烟气采样器 (崂应3072型,青岛崂应环境科技有限公司) 采集,采样材料为溶剂解析型活性炭采样管 (盐城尊科电子仪器有限公司) ,分A、B两部分装入100 mg和50 mg活性炭。在采集固定污染源VOCs时,将管路连接好,参照《固定污染源废气中挥发性有机物的测定 固相吸附-热脱附气相色谱-质谱法HJ 734-2014》[34]和《环境空气 苯系物的测定 活性炭吸附/二硫化碳解吸-气相色谱法 HJ 584-2010》[35],以0.5 L·min−1的流量采集20 min,采气10 L。采集完成后,立即用密封帽将样品两端密封,于4 ℃条件下避光保存、运输。
(2) 废气检测方法。将采样管中采集好的活性炭A段和B段取出,分别倒入10 mL磨口具塞试管中,每个试管中各加入1 mL异丙醇/二硫化碳混合解析液 (取98 mL二硫化碳,加入2 mL异丙醇,混匀) ,密闭,轻轻振动,在室温下解析1 h后取1 uL样品消解液注射到气相色谱-质谱联用仪 (岛津GCMS-2010SE,岛津 (上海) 实验器材有限公司) 中。
采用气相色谱-质谱联用仪进行废气组分分析,色谱柱为 SH-Rtx-5 石英毛管色谱柱(30 m×0.25 mm×0.25 μm),检测器为EI电子轰击源。扫描方式为全扫描,扫描范围为20~600 amu;离子化能量70 eV;柱流量1.80 mL·min−1。采用程序升温方法,设置初始温度为35 ℃,保持3 min,接着以10 ℃·min−1升至80 ℃,保持2 min,再以10 ℃·min−1升至280 ℃,保持15 min,然后以20 ℃·min−1升至320 ℃,保持2 min,分析时间总计48.5 min。不分流进样,进样量为1μL。载气为氦气,进样口温度270 ℃,离子源温度为260 ℃。
-
现场多效热回收直接催化燃烧装置进出口的VOCs质量浓度采用手持式VOCs检测仪 (PGM-7340型,华瑞科学仪器 (上海) 有限公司)测定,检测器为光离子化检测器。VOCs的处理效率以VOCs去除率为指标,计算方法如式(4)所示。
式中:
为装置的VOCs去除率;η 、Cin 分别为装置进气口、出气口处VOCs质量浓度,mg·m−3。Cout -
多效热回收催化燃烧装置废气风量为20 000 m3·h−1,系统流动速度稳定在4.63 m·s−1。通过质谱图检索识别,该基地的废气主要成分为乙醇、4-正丙基苯甲醛、α-蒎烯、十二烷、正十四烷、2,4-二叔丁基苯酚、十七烷、二十烷、姥鲛烷、二十酸甲酯、邻苯二甲酸二丁酯、二十一烷、二十二烷、间苯二甲酸二辛酯、植烷、三十二烷。废气组分成分如图4所示。根据GC-MS成分分析结果,制药厂排放的有机废气主要成分为乙醇,同时伴有其他烷类、酯类等有机化合物,VOCs成分如表1结果所示。
-
制药厂现场记录了2022年6月8日—10日多效热回收催化燃烧装置进气口和出气口VOCs质量浓度 (每隔3 min记录1次实验结果) (图5) 。这3 d内,进气口VOCs最低质量浓度为22 mg·m−3,最高质量浓度达到6 293 mg·m−3,相差286倍,数据波动大。这符合有机废气呈现间歇性排放的制药行业废气排放常见特征[36]。每日中午VOCs质量浓度较低,为24 h内最低区间值。这是由于该药厂采用传统的人工浇泼制药溶剂的方式,中午时间工人休息,暂停溶剂浇泼,但车间内还残余有机废气。每日下午16:15左右,VOCs质量浓度为当日峰值,此时段为车间最后一次浇泼制药溶剂时间,溶剂使用量也为一天中的最大值。
基于现场数据,分析工艺的处理能力和处理效率。在处理能力方面,设计的多效热回收的催化燃烧工艺可应对制药行业大流量、间歇性VOCs排放的特点;对比进气口、出气口VOCs质量浓度有明显降低,3 d内出气口VOCs质量浓度值均小于工厂限值 (20 mg m−3) ,并低于《制药工业大气污染物排放标准》(GB 37823—2019)对NMHC、TVOC、苯系物及某些危害大的特征污染物规定的排放限值[37]。通过预先定义的基于模糊PID的控制策略中比例、积分和微分系数,多效热回收催化燃烧装置能根据进气口VOCs质量浓度对补热回路中酒精摄入量进行自动调控,从而实现对多效热回收这样复杂工艺流程中温度的间接控制,进而有效控制出气口的VOCs质量浓度。在中午工人休息时间段,通过增加补热回路中酒精浓度的方式保证催化燃烧炉的正常工作,减少因启炉或电加热补热造成的成本和效率问题,可经济高效地解决因短时间工人休息或间歇性停产造成的排放处理稳定性问题,提高废气处理设备工作鲁棒性,从而提升废气处理能力。
在处理效率方面,现场VOCs处理综合处理效率 (去除率) 达97%以上,且VOCs处理效率受进气口质量浓度影响 (图5) 。当进气口VOCs质量浓度为22~27 mg·m−3时,VOCs处理效率为70%~80%;当进气口VOCs质量浓度为31~89 mg·m−3时,VOCs处理效率为80%~90%;当进气口VOCs质量浓度为98~178 mg·m−3时,VOCs处理效率为90%~95%;当进气口VOCs质量浓度大于180 mg·m−3,VOCs处理效率大于95%;当进气口VOCs质量浓度大于1 000 mg·m−3,VOCs处理效率能稳定达到98%以上。由于该系统使用基于模糊PID方法的控制策略,将催化燃烧炉的温度控制在300~400 ℃,当进气口VOCs质量浓度越高,催化燃烧炉内燃料量越大,燃烧释放热量更多,催化剂床层温度随之升高,从而有利于VOCs处理效率的提升。
-
3个检测日中得到的数据具有高度相似性。图6为该制药厂6月9日VOCs去除率随进气口VOCs质量浓度的变化。由于多效热回收催化燃烧工艺在补热回路中增加了酒精燃烧机进行补热,当进气口输入的VOCs质量浓度较低时,仍可保证催化燃烧炉的正常工作。
一方面,由于补热回路中酒精燃烧机的补热作用及基于模糊PID理论的控制策略,使得当进气口VOCs质量浓度较低时,去除效率不低于80%;另一方面,随着进气口质量浓度提高,多效热回收催化燃烧工艺VOCs去除率接近100%。此外,VOCs质量浓度和去除率关系散点被包含在2条指数函数曲线中。这2条曲线通过2阶指数函数拟合,测量值分布的上限和下限曲线表达式即式(5)和式(6)。
图6阐明了多效热回收催化燃烧工艺对VOCs去除率随进气口浓度的变化趋势。一方面,由于测量时新更换了催化燃烧炉内的催化剂,该函数体现了系统的理想去除能力,物理意义为系统在不同进气口浓度下的最大去除能力。通过测量某一时刻进气口质量浓度,并将其带入式(5)和式(6),可计算得到去除率。将计算得出的去除率和理想条件进行对比,可评估催化剂的催化能力,为催化剂的更换提供量化指标。另一方面,将离散的测量点转化成连续曲线,为后续催化燃烧的研究提供对比依据,并对装置的改进、升级和工艺设计优化提供数据基础。
-
将本工艺与同等处理规模的传统工艺“分子筛吸附+催化燃烧+喷淋”工艺进行对比,分析其运行经济性,结果见表2。
本工艺的运行成本主要包括:电费、滤材消耗、催化剂使用、危废处理、燃料消耗、自来水消耗。与“分子筛吸附+催化燃烧+喷淋”相比,本工艺无需使用吸附剂,没有人工费用,电费更低,能够实现自动化控制,在操作上也更简便。在考虑折旧等消耗后,按年运行4 800 h计算,得到本工艺的年平均运行成本为35.72 万元。与传统工艺相比,运行成本降低了至少27%。
-
1) 采用多效热回收的催化燃烧工艺能有效解决制药厂VOCs排放超标问题。现场数据证明,以蓄热、换热、回热和补热组成的多效热回收催化燃烧装置能解决制药企业大流量、间歇性VOCs排放问题。
2) 催化燃烧工艺和多效热回收装置对制药厂VOCs的综合处理效率大于97%。处理效率受进气口质量浓度影响,当进气口VOCs质量浓度大于1 000 mg·m−3时,VOCs处理效率能稳定达到98%以上。随着进气口VOCs质量浓度的提高,VOCs处理效率接近100%。
3) 与传统“分子筛吸附+催化燃烧+喷淋”工艺相比,多效热回收催化燃烧工艺无需使用吸附剂,没有人工费用,电费更低,能实现自动化控制,操作也更为简便。本工艺的年平均运行成本为35.72 万元。与传统工艺相比,运行成本降低了至少27%。
4) 由于催化燃烧和多效热回收过程很难用线性模型进行模拟,处理间歇性有机废气的排放问题不能根据实时排放状态进行精准补热,但针对燃烧过程和多效热回收流程的分段精细化建模能进一步提升处理效率,并降低成本。
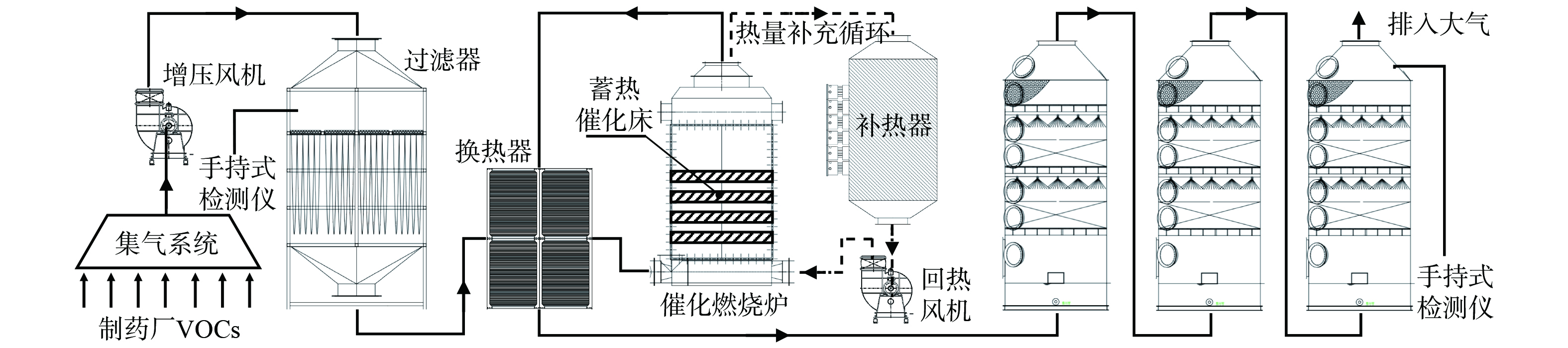