催化湿式氧化处理助剂废水工程及过程模拟
Engineering and process simulation of auxiliary wastewater treated by catalytic wet air oxidation
-
摘要: 助剂废水是一种高浓度难降解有机废水,以催化湿式氧化(CWAO)为主体的CWAO-UASB-AOA-接触氧化-混凝沉淀工艺能够对其进行有效降解。在CWAO工业化装置设计中,床层温升(Tg)和换热器总传热系数(K)是换热器设计的2个重要参数。采用Aspen Plus对CWAO过程进行稳态模拟,Aspen Plus对Tg模拟结果同分布式控制系统(DCS)实测结果相对误差在±2.0%以内。根据计算结果可知,K为800 W · (m2 · °C)-1。结合K和Tg可以用来估算换热面积,进而指导CWAO过程系统工程的工业化设计。Abstract: Auxiliary wastewater is a kind of wastewater containing high-concentration and hard-degraded organic pollutants. Catalytic wet air oxidation (CWAO) is the main process of CWAO-UASB-AOA-contact oxidation-coagulation method, which can effectively treat hard-degraded organic pollutants in auxiliary wastewater. In this CWAO industrialization apparatus, the temperature gradient between the reactor inlet and outlet (Tg) and heat transfer coefficient (K) are two important parameters for heat exchanger design. To this end, we carried out the steady-state simulation of CWAO process by Aspen Plus, and revealed that the relative error Tg of between the simulation and testing results of distributed control system (DCS) was less than 2.0%. Then, the K factor was calculated to be 800 W · (m2 · °C)-1. As a consequence, the heat exchanger area was readily estimated in term of Tg and K, and then provided an insightful engineering design guideline of CWAO industrialization system.
-
-
[1] 钟璟,韩光鲁,陈群.高盐有机废水处理技术研究新进展[J]. 化工进展,2012,31(4):920-926 [2] ARENA F, DICHIO R, GUMINA B,et al.Recent advances on wet air oxidation catalysts for treatment of industrial wastewaters[J].Inorganica Chimica Acta,2015,431:101-109 10.1016/j.ica.2014.12.017 [3] MISHRA V S, MAHAJANI V V, JOSHI J B.Wet air oxidation[J].Industrial & Engineering Chemistry Research,1995,34(1):2-48 10.1021/ie00040a001 [4] 蔡先明,秦侠,张丽,等.催化湿式氧化法处理垃圾渗滤液[J].环境工程学报,2016,10(1):189-193 [5] 柏亚成,陈晔.高浓度苯酚废水的均相催化湿式氧化研究[J].现代化工,2015,35(6):136-138 [6] 雷燕, 雷必安, 杨其文, 等.催化湿式氧化处理城市污水厂污泥的研究进展[J].现代化工,2015,35(3):41-44 [7] 韩玉英.催化湿式氧化吡虫啉农药废水Cu/Mn催化剂稳定性[J].陕西科技大学学报(自然科学版),2012,30(4):42-45 [8] 曾经,彭青林.催化湿式氧化技术处理高浓度有机废水的研究[J].中国给水排水,2010,26(19):99-102 [9] 习成成,桑培伦,姜玲,等.Ru/TiO2催化湿式氧化废离子交换树脂技术研究[J].环境科学与技术,2017,40(6):104-109 [10] 刘俊,曾旭,赵建夫.NaOH强化催化湿式氧化处理制药污泥[J].化工环保,2017,37(1):106-109 [11] 龙辉.均相催化湿式空气氧化连续处理高含盐高浓度有机废水[D].杭州:浙江大学,2015 [12] 王思远.基于Aspen plus的高温甲烷化流程模拟及能量分析[D].上海:华东理工大学,2017 [13] 华宇瑞,龚志军,张智羽,等.基于流化床的煤部分气化ASPEN PLUS模拟[J].煤炭技术,2016,35(1):310-311 [14] 刘利平,王恒,方书起,等.Aspen Plus软件模拟生物油模化物水蒸气重整制氢热力学[J].计算机与应用化学,2016,33(3):330-334 [15] 柏静儒,白章,王擎,等.基于Aspen Plus的桦甸式油页岩干馏工艺系统模拟[J].化工学报,2012,63(12):4075-4081 [16] 贾晓华.Aspen plus在真空制盐蒸发中的模拟应用[J].盐科学与化工,2017,46(3):8-13 [17] 汪晓军,肖锦.有机废水的热值及焚烧处理能耗分析[J].环境工程,1990,8(6):9-11 -
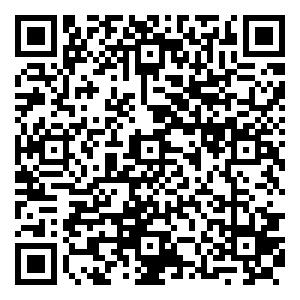
计量
- 文章访问数: 4220
- HTML全文浏览数: 4013
- PDF下载数: 183
- 施引文献: 0