污泥低温干化过程中硫的转化与分布
Sulfur transformation and distribution in the low temperature drying process for sludge
-
摘要: 为研究污泥低温干化过程中的含硫气体释放和系统中硫的转化,以一条产线为例,检测讨论污泥干化全过程中硫含量、气体中含硫污染物浓度和气体冷凝水中硫化物浓度和分配情况。经测试发现,污泥低温干化过程中,干污泥中最终保留80%以上的硫元素并随着干污泥进入电厂煤棚,其余硫元素在干化过程中转化成气态、固态。检测发现,干燥过程中有硫化氢、甲硫醚、二硫化碳等气体逸出,并在工艺过程中发生归中反应,凝结出硫单质进入冷凝污水或附着在管道内壁上,硫单质为硫总量的12.5%;管道内壁上固体附着物质含硫量达到54%。研究结果为污泥低温干化过程提供元素硫的转化分布数据,对污泥干化系统设备维护保养、气体环保处置、含硫物质的回收处理具有积极意义。Abstract: In this study, the sulfur-containing gas release and sulfur transformation in the sludge low-temperature drying system were investigated. In a production line for sludge low-temperature drying process, the total sulfur content in sludge, and the concentration and distribution of sulfur-contained pollutants in gas and condensate water were tested. The results show that over 80% sulfur element remained in dried sludge during the drying process, finally transported to the power plant and mixed with coal for incineration, the rest of sulfur element transformed into gaseous or solid states. Some kinds of gas, such as hydrogen sulfide, methionine, carbon disulfide ect., could escape during the drying process, and the synproportionation reaction occurred accordingly. The condensed sulfur entered the sewage, or adhered to the pipeline inner wall which could account for 12.5% of the total sulfur. The attachment on the pipeline inner wall contained 54% sulfur. In this study, the sulfur element transformation and distribution have been provided for sludge low-temperature drying process, which is of great significance for sludge drying system equipment maintenance, gas environmental treatment and sulfur-contained substances recovery.
-
Key words:
- sludge /
- low temperature drying /
- hydrogen sulfide /
- sulfur transformation
-
-
[1] 戎静.上海城市污水厂污泥处置现状研究[J].环境科学与管理,2016,41(4):94-97 [2] 段妮娜.污泥厌氧消化系统中硫转化的主要途径及影响因素[J].环境工程,2017,35(12):129-133 [3] 杨真乐,乔瑜,刘帅等. 污泥低温热解过程中含硫气体释放实验研究[J]. 工程热物理学报,2012,33(12):2202-2206 [4] 俞益辉,张宝茸.污泥低温干化污染物排放及环境影响研究[J].污染防治技术,2015,28(5):24-26 [5] 孙明华,王凯军,张耀峰,等.污泥干化协同焚烧的环境影响实例研究[J].环境工程,2016,34(3):128-132 [6] 范海宏,张诗洋,李斌斌,等. 污泥干化过程中含硫气体的抑制研究[J].硅酸盐通报,2017,36(3):888-892 [7] 岳宝,张耀峰. “二段法”干化工艺在中国城市污泥处置中的应用和实践[J].环境工程,2015,33(2):88-91 [8] 煤炭科学研究总院煤炭分析实验室. 煤中全硫的测定方法:GB/T 214-2007 [S]. 北京:中国标准出版社,2008 [9] 沈阳环境科学研究所.空气质量 硫化氢、甲硫醇、甲硫醚和二甲二硫的测定 气相色谱法:GB/T 14678-1993 [S].北京:中国标准出版社,1993 [10] 北京市机电研究院环境保护技术研究所. 空气质量 二硫化碳的测定 二乙胺分光光度法:GB/T 14680-1993 [S].北京:中国标准出版社,1993 [11] 北京市环境保护监测中心. 固定污染源废气 硫酸雾的测定 离子色谱法:HJ 544-2016 [S]. 北京:中国环境科学出版社,2016 [12] 甘肃省环境监测中心站. 水质 无机阴离子(F-、Cl-、NO2-、Br-、NO3-、PO43-、SO32-、SO42-)的测定 离子色谱法:HJ 84-2016 [S].北京:中国环境科学出版社,2016 [13] ATTAR A.Chemistry, thermodynamics and kinetics of reactions of sulfur in coal-gas reactions: Review[J].Fuel, 1978,57(4):201-212 10.1016/0016-2361(78)90117-5 [14] YAN J D, YANG J L, LIU Z Y.SH radical: The key intermediate in sulfur transformation during thermal processing of coal [J].Environmental Science & Technology, 2005, 39(13):5043-5051 10.1021/es048398c [15] KHAN M R.Prediction of sulfur distribution in products during low-temperature coal pyrolysis and gasification[J].Fuel,1989, 68(11):1439-1449 10.1016/0016-2361(89)90043-4 -
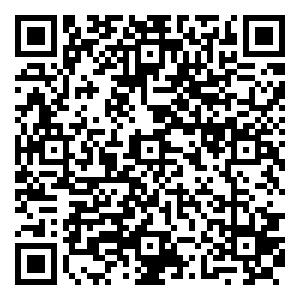
计量
- 文章访问数: 4270
- HTML全文浏览数: 4104
- PDF下载数: 134
- 施引文献: 0