高含碳金属化球团制备及对焦化废水的处理
Preparation of high carbon-bearing pellets and research on its treating results of coking wastewater
-
摘要: 针对传统微电解填料昂贵、生产成本高的问题,利用冶金废弃粉尘制备微电解填料。分析了碳氧比(C/O)、还原时间、还原温度对微电解填料的化学成分、强度性质的影响,并对微电解填料的空隙率、表面形貌进行了实验研究。结果表明:在1 300 ℃,C/O为1.0,还原时间20 min的条件下制备的高含碳金属化球团满足微电解填料性能要求,为最佳制备工艺。同时,利用高含碳金属化球团对焦化废水处理进行了实验研究,COD去除率可达63%,B/C值明显提高,提高了废水的可生化性。Abstract: Micro-electrolysis filler was made from metallurgical waste dust to solve the problem of high production cost. The influences on chemical composition and strength properties of micro-electrolysis filler was analyzed by different process parameters such as C/O, reduction time and reduction temperature. The void friction and surface amplification of micro-electrolysis filler were also studied. The results indicate that under the condition of reduction temperature of 1 300 ℃, C/O of 1.0 and reduction time of 15 min, the preparation technology of high carbon-bearing pellets meet the actual requirements. In the test of the treatment of coking wastewater, the COD removal rate can up to 63%, B/C increased significantly and improved the wastewater biodegradability.
-
-
[1] 崔志刚,李浩,王宗廷. 微电解法处理废水研究进展[J]. 山东化工,2009,38(4):21-24 [2] 曹立伟,张淑娟,张有智,等. 微电解填料的研究进展[J]. 现代化工,2015,35(6):13-17 10.16606/j.cnki.issn0253-4320.2015.06.043 [3] 宋忠忠,李杰,孙静. 铁碳微电解填料的研究及应用现状[J]. 绿色科技,2017(6):48-50 10.16663/j.cnki.lskj.2017.06.016 [4] 曹飞. 新型微电解填料制备及其性能研究[D]. 镇江: 江苏大学,2016 [5] LIU B C, DAI S H, SHEN F M, et al.Metallurgical characteristic of carbon-proportioning pellets mixed with Zn-bearing electric arc furnace dust[J].Journal of Northeastern University,2004,25(5):431-434 [6] 马兴亚,汪琦,姜茂发. 含碳球团还原技术研究现状[J]. 烧结球团,1999,5(3):24-26 [7] 牛永胜,马永磊,李惠朝,等. 含碳球团配碳比的试验研究[J]. 河北冶金,2001,2(2):8-11 [8] 胡凌标. 热脱发微碳铬铁工艺过程中熔体的化学物理变化及Cr2O3还原因素浅析[J]. 铁合金,1996(2):5-11 [9] 吕庆,刘卫东,赵利国,等. 含碳球团还原的显微观察[J]. 河北理工学院学报,2001,23(4):19-24 [10] 张家驹. 铁冶金学[M]. 沈阳: 东北工学院出版社,1987:42 [11] 张晓伟. 微电解陶粒在染料模拟废水处理方面的应用[D]. 济南: 山东大学,2013 [12] 周璇. 铁炭陶粒微电解填料的开发与应用研究[D]. 天津:天津大学,2010 [13] 张春永. 铁炭微电解法废水处理技术研究[D]. 南京: 东南大学,2004 -
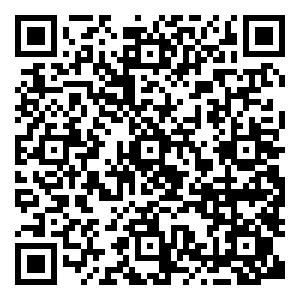
计量
- 文章访问数: 4233
- HTML全文浏览数: 3736
- PDF下载数: 489
- 施引文献: 0