超声降解水中的磺胺嘧啶
Degradation of sulfadiazine by ultrasonic
-
摘要: 以磺胺嘧啶(SD)为研究对象,探讨了超声功率、初始浓度、pH值以及超声协同H2O2、Fenton、TiO2等组合工艺对超声降解SD效率的影响。实验结果表明,超声可有效降解水中低浓度的SD,尤其在酸性条件下,超声降解更为显著,降解过程遵循准二级反应动力学模型。加入H2O2或TiO2可在一定程度上促进SD的超声降解,加入Fenton试剂则显著提升SD的去除率。依据量化计算以及LC-MS测定结果,探讨了SD的超声降解机理。超声降解水中SD主要是基于·OH自由基的氧化过程。Abstract: The effects of ultrasonic power, initial concentrations, solution pH values and addition of oxidant H2O2, Fenton reagent, TiO2 on the degradation efficiency of SD by ultrasonic(US) were studied. Experimental results show that low-concentration SD can be effectively removed by ultrasonic in aqueous solution, the removal efficiencies can be remarkably enhanced in acidic solution, and the degradation of SD was in accordance with the pseudo-second-order kinetic model. In addition, H2O2 and TiO2 can promote ultrasonic induced degradation of SD to a certain extent. However, SD removal can be markedly improved with the addition of Fenton reagent. The degradation mechanism of SD was supposed by results of quantum chemical calculations and LC-MS. Ultrasonic induced degradation of SD is mainly ascribed to ·OH oxidation.
-
Key words:
- ultrasonic /
- degradation /
- sulfadiazine /
- mechanism
-
垃圾焚烧技术由于具有高效减容减量和回收热量等优点,促使我国垃圾焚烧产业迅速发展,已成为我国生活垃圾无害化处置的主流方式之一。飞灰是垃圾焚烧过程中不可避免的副产物,富集了高浓度重金属、二噁英类物质和金属氯盐[1],属于典型的危险废物。随着垃圾焚烧技术的进一步推广,2020年我国飞灰预计产量突破1×107 t[2]。当前,飞灰的主流处理工艺是水泥固定/稳定化后填埋,然而这种传统的处理方式存在二次污染风险高、占用大量宝贵的土地和资源化利用率低等缺点。在面对新建填埋场“邻避效应”、土地短缺和资源匮乏的三重压力下,迫切需要开发非填埋式的飞灰无害化和资源化技术。
目前,国内外利用垃圾焚烧飞灰生产水泥[3]、陶粒[4]等建材的研究已成热点。ZHAN等[5]发现,将垃圾焚烧飞灰水洗后混合原始飞灰投加到共烧结体系中可烧制出密度等级为800级的轻质陶粒,飞灰集成利用率达到了41.4%。但是,通常焚烧飞灰中的Ca/Si比例较大,CaO含量过高不利于陶粒烧成,需要添加SiO2和Al2O3物质。因此,有学者通过掺加粉煤灰、废玻璃和膨润土等高Si、Al质的组分作为焚烧飞灰原料中的Si和Al含量的补充[5-6]。基于污泥富含Si和Al盐的特性,本研究拟尝试以污泥作为垃圾焚烧飞灰制备陶粒过程的Si和Al调节剂,在解决飞灰无害化和资源化利用问题的同时,实现污泥的消纳。
水热技术是当前处理垃圾焚烧飞灰的新兴方式,对飞灰中的Cl、Na、K和Ca均具有一定的去除效果[7];且在强化的条件下,可实现重金属的大幅稳定以及高达90%的二噁英脱除率[8-9]。污泥热解炭化是指在绝氧条件下对污泥进行加热处理,以获得可再利用的生物炭、油和可燃气的技术,目前已成为城市污泥的无害化和资源化处理处置研究的热点技术之一[10-11]。已有研究[12-13]证明,污泥辅助飞灰水热耦合热解处理能够避免飞灰烧结,且在一定程度上能够强化飞灰的重金属固化和二噁英分解脱毒。因此,本研究采用污泥辅助水热耦合热解的方法实现飞灰的脱毒脱氯,同时为飞灰补充Si和Al源,以此脱氯脱毒飞灰作为陶粒制备的原料,旨在探索一条飞灰和污泥协同资源化利用的途径。
1. 材料与方法
1.1 供试原料
本研究使用的生活垃圾焚烧飞灰来源于东莞市某生活垃圾焚烧厂。该厂生活垃圾处理规模为1 500 t·d−1,烟气处理工艺为“SNCR法脱硝+PNCR法脱硝+半干法脱酸+活性炭+布袋除尘”,飞灰产生于烟气净化过程。采集的飞灰经105 ℃烘干后备用。脱水污泥取自厦门市某污水处理厂,含水率为76.52%,置于4 ℃冷藏保存。
所用硝酸(HNO3)、氢氟酸(HF)、高氯酸(HClO4)和冰醋酸(CH3COOH)等为优级纯,购自国药集团化学试剂有限公司;盐酸羟胺(NH2OH·HCl)为分析纯,购自国药集团化学试剂公司;30%过氧化氢(H2O2)和醋酸铵(CH3COONH4)为分析纯,购自西陇科学股份有限公司;多元素标准溶液(GSB 04-1736-2004)采自国家有色金属及电子材料分析测试中心。实验用水为超纯水。
1.2 脱氯脱毒飞灰的制备与表征
首先,将脱水污泥和飞灰按质量比4∶1(干基)混合加入到水热反应釜(FCF-2L,中国),加水调节液固比至4∶1;然后,将反应釜密封,升温至水热温度180 ℃,在缺氧条件下水热反应60 min,并以200 r·min−1的转速搅拌;反应结束后,将水热产物固液分离,并将分离出的固体产物在105 ℃烘干至恒重,获得水热固相;之后,将水热固相破碎,装入石英反应管,在氮气气氛下热解60 min,热解温度为800 ℃,升温速率为15 ℃·min−1;热解结束后,在氮气保护下冷却,获得热解残渣;最后,将热解残渣研磨过100目筛(记为P25),以此作为陶粒制作原料。
分别参照危险废物浸出毒性鉴别标准(GB 5085.3-2007)[14]附录F和水平振荡法 (HJ 557-2010)[15]方法对P25的可溶性氯含量和重金属浸出浓度进行测试。利用X射线荧光光谱仪(XRF,PANalytical Axios-mAX,荷兰)和热重分析仪(TGA,NETZSCH TG 209 F3,德国) 分别对P25的化学组成和热失重特征进行分析。
1.3 陶粒制备和性能分析
按水料比1.20~1.50充分混合P25和去离子水,手工搓制成直径为6~8 mm的生料球,105 ℃干燥5 h后,送入马弗炉(QSH-1700M,中国)烧制成陶粒。升温速率为10 ℃·min−1,煅烧温度设定为1 150、1 175、1 200、1 225和1 250 ℃,煅烧停留时间为0、5、10、20和30 min。依据煅烧条件对获得的陶粒样品进行命名,如表1所示。
表 1 陶粒样品命名和煅烧条件Table 1. Nomenclature of ceramsite samples and sintering conditions样品 煅烧温度/℃ 煅烧时间/min C1 150-20 1 150 20 C1 175-20 1 175 20 C1 200-20 1 200 20 C1 225-20 1 225 20 C1 250-20 1 250) 20 通过扫描电子显微镜(SEM,Hitachi S-4800,日本)和X射线衍射仪(XRD,PANalytical X’Pert Pro,荷兰)对陶粒形貌和晶相结构进行分析。陶粒的堆积密度、表观密度、吸水率和氯化物含量的测定参照国家标准《轻集料及其试验方法》(GB/T 17431.22010)[16],Cl−浓度采用离子色谱(DIONEX ICS-3000,美国)进行检测。S元素质量分数采用元素分析仪(EA,Elemantar Vario EL cube,德国)进行分析。抗压强度采用万能材料电子试验机(ZL-8001,中国)进行测试,按照式(1)计算单颗粒抗压强度[17],以6颗抗压测试平均值作为测试结果。
σ=2.8P/(πd2) (1) 式中:σ为单颗粒抗压强度,MPa;P为陶粒破碎最大瞬时压力,N;d为陶粒垂直承压面的直径,mm。
1.4 重金属分析方法
将陶粒破碎过100目筛。取0.10 g样品置于聚四氟乙烯管,经混酸体系(HNO3∶HF∶HClO4= 6∶3∶2)消解后用于重金属总量测定。
采用BCR三步连续提取法[18]和醋酸缓冲溶液法(HJ/T 300-2007)[19]分别提取重金属存在形态和浸出毒性,提取后采用电感耦合等离子质谱仪(ICP-MS,Agilent 7500CX,USA)进行检测。其中,重金属形态分为4种:可交换态(F1)、可还原态(F2)、可氧化态(F3)和残渣态(F4)。
应用潜在生态风险指数(RI)评价陶粒中重金属的潜在风险,计算公式[20]如式(2)~式(4)所示。
Cf=Ci/Cn (2) Er=Tr×Cf (3) RI=ΣEr (4) 式中:Cf为单一重金属污染指数;Ci、Cn分别代表各类重金属(F1+ F2+ F3)态和F4态组分质量分数,mg·kg−1;Tr表示毒性响应因子,分别为Ni(6)、Co(5)、Cu(5)、Pb(5)、Cr(2)、Mn(1)、Zn(1);Er为单项潜在生态风险系数。
2. 结果与分析
2.1 P25表征
P25的可溶性氯含量为0.341%,低于《生活垃圾焚烧飞灰污染控制技术规范(试行)》(HJ 1134-2020)[21]规定的2%阈值;按照HJ 557-2010[15]制备的浸出液中含有Mn、Ni、Cu、Zn、Cd和Pb等重金属,如表2所示;其浸出浓度不超过《污水综合排放标准》(GB 8978-1996)[22]评定限值。因此,P25的可溶性氯含量和重金属浸出满足HJ 1134-2020[21]对飞灰处理产物的污染控制要求,可作为烧制原料制备陶粒。
表 2 P25的重金属浸出浓度Table 2. Heavy metal leaching concentration of P25mg·L−1 重金属 浸出浓度 GB 8978-1996限值[22] Mn 0.194 2.01) Ni 0.022 1.02) Cu 0.047 0.51) Zn 0.041 2.01) Cd 0.001 0.12) Pb 0.010 1.02) 注:1)为按照第二类污染物最高允许排放浓度按照一级标准执行;2)为按照一类污染物最高允许排放浓度执行。 热重曲线如图1所示,P25最大失重峰位于499 ℃,虽然在350~600和770~1 000 ℃区间内发生了明显的质量损失,但其质量损失率分别仅为2.87%、2.12%,整体质量损失不超过5%。这表明,P25的结构水和有机质等挥发组分含量极低[23],烧制陶粒理论上可以省去工艺中的预热环节。
污泥、飞灰和P25的元素分析结果列于表3。如表3所示,P25的SiO2 质量分数(25.2%)低于Riley三相图[24]所示黏土烧胀相应范围(53%~79%)的下限,Al2O3质量分数(20.2%)恰好位于要求范围(10%~25%)之内,而其他助熔与产气成分(Na2O、K2O、MgO、CaO、FeO、Fe2O3等)组分总量则较理想范围(13%~26%)略偏高。P25的Si和Al含量远高于原始飞灰,而CaO和Cl含量显著降低。因此,通过污泥辅助水热-热解可大大改善飞灰作为陶粒烧制原料的特性。
表 3 污泥、飞灰和P25的元素分析Table 3. Chemical components analysis of sludge, fly ash and P25% 化学成分 污泥 飞灰 P25 SiO2 24.06 3.51 25.24 Al2O3 16.28 0.81 20.18 Na2O 0.88 9.80 1.38 MgO 1.41 1.09 2.39 K2O 1.41 5.64 1.30 CaO 3.42 44.72 16.21 Fe2O3 17.91 0.89 12.58 Cl 0.56 24.53 2.30 P2O5 10.20 0.30 10.67 SO3 3.056 6.20 2.89 2.2 陶粒性能分析
由图2(a)和2(b)可知,随着煅烧温度的升高,陶粒的抗压强度、堆积密度和表观密度呈现先增大后减少的趋势;吸水率则呈逐渐下降趋势。本研究采用球形陶粒的单颗粒抗压强度替代《轻集料及其试验方法》(GB/T 17431.1-2010)[25]中轻粗集料筒压强度,其值可折合为筒压强度的0.9倍[26-28]。由此判断,1 150 ℃烧制的陶粒吸水率(42.5%)过高而抗压强度(0.68 MPa)过低,不符合国家标准;而1 200、1 225和1 250 ℃烧制的陶粒的堆积密度和抗压强度分别为1 183、1 066、898 kg·m−3和15.0、19.3、10.6 MPa,远超过了GB 17431.1-2010密度等级900级高强轻粗集料所对应的筒压强度6.5 MPa(折合抗压强度约5.85 MPa)的要求,属于高强陶粒。煅烧时间的影响(图2(c)和2(d))相对较小,当煅烧时间超过10 min,各项指标趋于稳定。
如表4所示,经1 200 ℃高温烧结的陶粒其水溶性Cl含量低于0.000 5%,S含量则低于0.22%,分别达到了GB/T 17431.1-2010[25]中有害物质氯化物含量≤0.02%及硫化物和硫酸盐含量≤1.0%的要求。
表 4 不同温度烧制陶粒的有害物质含量Table 4. Hazardous substances content of ceramsite at different sintering temperature% 供检有害物质 P25 C1 175-20 C1 200-20 C1 225-20 C1 250-20 Cl (以Cl−计) 0.014 9 0.003 9 0.000 5 0.000 4 0.000 3 S (以SO3计) 3.431 0.211 5 0.129 0 0.164 3 0.174 8 以上结果表明,当烧制温度达到1 200 ℃,陶粒的抗压强度(≥10 MPa)、吸水性(≤10%)、堆积密度(≤1 200 kg·m−3)、氯化物含量(≤0.000 5%)、硫化物和硫酸盐含量(≤0.22%)均符合国家标准(GB/T 17431.1-2010)[14];而且,在1 250 ℃烧制20 min后,可以制备出优质高强陶粒(密度等级为900级)。
2.3 陶粒微观结构分析
从形貌变化上看(图3),随着烧结温度从1 150 ℃升高至1 250 ℃,P25中的松散颗粒逐渐粘结形成致密块体。该变化可以通过液相烧结机理[29-30]来解释。当温度高于1 150 ℃,原料中低熔点组分开始熔融,形成的液相填充未熔颗粒之间的空隙,导致未熔颗粒相互紧密粘合,进而,胚体体积发生收缩,陶粒的密实度和抗压强度急剧升高,吸水率便出现下降;当煅烧温度达到1 200 ℃时,陶粒体积收缩最为明显,平均粒径最小,此时陶粒容重到达最大值;而抗压强度的峰值出现在1 225 ℃,这是因为当温度超过1 200 ℃,陶粒的结晶度进一步提高,故观察到陶粒的表面产生了釉面光泽,说明玻璃相形成于陶粒表面[23],这有利于进一步增强抗压强度以及维持低的吸水率。与此同时,陶粒表层颜色由棕红色(1 200 ℃)向棕黑色(1 225 ℃)过渡直到转变为亮黑色(1 250 ℃),用放大镜观察到了釉面的小气孔及陶粒内部随温度升高而愈显发达的孔隙结构,这是因为Fe2O3在高温下解离释放气体并且产生了黑色Fe3O4[29]。孔结构的产生造成机械强度和密度减小。
P25与陶粒的XRD鉴定结果(图4)显示,高温烧结后,陶粒中的晶相发生分解与重构。P25中的SiO2、氯磷灰石(Ca10Cl2(PO4)6)消失,陶粒中检测出的主要晶相为Fe2O3、铝硅酸钙(CaAl2Si2O8)和磷钙钴矿(Ca2.6Co0.4(PO4)2)。铝硅酸钙(CaAl2Si2O8)的形成是由于飞灰中CaO成分的存在,其参与了陶粒烧结过程的固-液相反应;此外,因污水污泥中含有丰富的P元素,飞灰和污泥经适当的水热耦合热解高温处置形成了结晶性氯磷灰石(Ca10Cl2(PO4)6)。磷灰石族矿物被视为最稳定的磷酸盐矿物相,能够通过同构取代捕获二价重金属阳离子,如Pb2+、Co2+取代Ca2+,因而,在热处理过程中有助于抑制重金属的挥发[31-32]。
2.4 陶粒中重金属的浸出毒性和形态分布
1) 浸出毒性。如表5所示, P25原料和4种不同温度烧结陶粒中各项重金属的浸出浓度均低于GB 5085.3-2007[14]规定的限值。随着陶粒烧结温度的升高,陶粒中Mn、Co、Ni、Cu、Zn和Pb等重金属的浸出毒性升高;尤其是当烧结温度达到1 250 ℃时,Zn的浸出毒性高出P25的500倍。这些结果表明,过高的烧结温度可能使重金属得到部分活化,浸出毒性增加。
表 5 P25和不同温度烧制陶粒的重金属浸出Table 5. Heavy metal leaching concentration of P25 and ceramsite sintered at different temperaturesmg·L−1 重金属 P25 C1 175-20 C1 200-20 C1 225-20 C1 250-20 GB 5085.3-2007标准值[14] Cr 0.014±0.001 0.002±0.00 0.001±0.00 0.001±0.00 N.D. 15 Mn 323.6±12.60 14.75±0.180 19.30±0.278 38.16±1.785 76.78±0.663 — Co 0.020±0.012 0.006±0.00 0.008±0.00 0.027±0.00 0.083±0.001 — Ni 0.046±0.017 0.007±0.004 0.004±0.00 0.012±0.00 0.033±0.001 5 Cu N.D. 9.191±0.313 7.892±0.283 12.51±0.338 15.00±0.073 100 Zn 0.099±0.027 0.091±0.001 0.264±0.032 1.451±0.064 54.32±0.900 100 Pb N.D 0.001±0.00 0.001±0.00 0.002±0.00 0.002±0.00 5 注:N.D.表示未检出。 2) 形态分布。陶粒中重金属BCR形态分析结果(图5)表明,P25中的Cr、Mn、Co和Ni等重金属的存在形态主要为F1态,分别占38%、41%、72%和71%;而Cu、Zn和Pb以F4态为主,分别占68%、84%和93%。高温烧结后,陶粒中各类重金属的F4态占比均超过了85%。但是,随着烧结温度升高,陶粒中Cr、Mn、Co、Cu、Zn和Pb的F1态占比有不同程度的增加,当烧结温度为1 250 ℃时,Cr、Cu、Zn 和Pb的F1态占比分别为4.5%、6.0%、9.4%和3.0%。其原因可能在于,Cl元素在陶粒烧制过程中通过氯化作用于重金属,使之转化为属于F1态的易挥发性重金属氯化物[33-36]。此外,各类重金属的活化程度具有明显的温度关联性,这可能与给定温度下含氯化合物释放Cl的能力和金属对Cl的亲和力有关[37]。
2.5 陶粒潜在生态风险评价
重金属潜在生态风险评价结果(表6)显示,随着烧结温度的升高,陶粒的值和RI值略有上升,但均处于轻微水平(Er<40,RI<50),表明其在应用过程中重金属潜在生态风险低。
表 6 陶粒的重金属潜在生态风险评价Table 6. Ecological risk assessment of heavy metals in ceramsite sintered at different temperatures样品 Er值 RI值 潜在生态风险程度 Cr Mn Co Ni Cu Zn Pb C1 175-20 0.01 0.00 0.02 0.11 0.00 0.00 0.09 0.23 轻微 C1 200-20 0.02 0.00 0.04 0.12 0.09 0.01 0.07 0.36 轻微 C1 225-20 0.07 0.00 0.19 0.43 0.29 0.03 0.43 1.45 轻微 C1 250-20 0.13 0.01 0.37 0.29 0.53 0.14 0.33 1.79 轻微 3. 讨论
在热处理过程中,重金属的挥发性或稳定性取决于温度[31]。陶粒BCR分析结果(图5)表明,高温烧结重金属F4态大幅增加,有利于重金属的稳定化,这可能与高温烧结过程铝硅酸盐和磷酸盐矿物的形成和生长有关。XRD结果(图4)证实,陶粒中存在铝硅酸钙(CaAl2Si2O8)和磷钙钴矿(Ca2.6Co0.4(PO4)2)。一方面,低熔点的铝硅酸钙在烧结过程中充当粘结剂[38],促进了液/固相反应进程,可将重金属原子包熔进无机矿物相基体,如硅酸盐、玻璃相等性质稳定的高强结构,从而增强陶粒中重金属的固化和稳定性;另一方面,陶粒中的重金属,如Pb、Zn和Cu,在热处理过程中通过离子交换、络合等作用,与共存的磷酸根和Ca元素结合形成高度热稳定的配合物,如磷钙钴矿的生成,也可在一定程度上稳定重金属[39]。
但是,当烧结温度从1 150 ℃升至1 250 ℃,重金属浸出毒性和F1态的占比显著增加,意味陶粒中的重金属发生活化,这可能是因为:1) 过高的温度促使稳定的无机矿物(硅酸盐)发生分解,Ca-Al-Si骨架结构遭到破坏,这与XRD检测结果一致(CaAl2Si2O8和Ca2.6Co0.4(PO4)2峰强度减弱);2) 高温环境使化学性质活泼的氯原子插进晶体内部,引起晶格破裂[36, 40],破坏稳定的重金属物种。
4. 结论
1) 污泥辅助飞灰水热-热解处置产物在1 175 ℃以上、焙烧20 min,可获得抗压强度、吸水率、堆积密度、氯化物含量、硫含量等指标均满足国家标准GB/T 17431.1-2010相应指标的要求的陶粒制品。其中,1 200~1 250 ℃烧制出了密度等级900~1 200级高强陶粒。
2) 高温焙烧过程中形成铝硅酸钙和磷灰石矿物在重金属固化过程中发挥重要作用。陶粒重金属浸出毒性低于GB 5085.3-2007标准阈值,重金属主要形态为F4态,占比超过85%,重金属潜在生态风险处于轻微水平(Er<40,RI<50)。
3) 重金属在过高的煅烧温度下发生部分活化,浸出毒性增加,F1态占比明显增加,其主要原因可能在于高温与Cl元素共同作用破坏稳定的晶体结构。
4) 以污泥辅助飞灰水热-热解处置产物为原料制备陶粒是实现飞灰资源化处置有效途径之一。
致谢:感谢中国科学院城市环境研究所仪器中心在表征和测试方面提供的技术支持;感谢余广炜、赖登国等在本研究中给予的宝贵意见。
-
[1] 徐维海, 张干, 邹世春, 等.典型抗生素类药物在城市污水处理厂中的含量水平及其行为特征. 环境科学, 2007, 28(8):1779-1783 Xu Weihai, Zhang Gan, Zou Shichun, et al. Occurrence,distribution and fate of antibiotics in sewage treatment plants. Environmental Science, 2007, 28(8):1779-1783(in Chinese) [2] 李彦文, 莫测辉, 赵娜, 等.菜地土壤中磺胺类和四环素类抗生素污染特征研究. 环境科学, 2009, 30(6):1762-1766 Li Yanwen, Mo Cehui, Zhao Na, et al. Investigation of sulfonamides and tetracyclines antibiotics in soils from various vegetable fields. Environmental Science, 2009, 30(6):1762-1766(in Chinese) [3] Richardson B. J., Lam P. K. S., Martin M. Emerging chemicals of concern: Pharmaceuticals and personal care products (PPCPs) in Asia, with particular reference to Southern China. Marine Pollution Bulletin, 2005, 50(9): 913-920 [4] 张丽佳, 刘承帅, 吴长安, 等. α-MnO2/水界面磺胺嘧啶的氧化降解动力学. 生态环境, 2008, 17(2): 471-477 Zhang Lijia, Liu Chengshuai, Wu Changan, et al. The oxidative degradation of sulfadiazine at the interface of α-MnO2 and water. Ecology and Environment, 2008, 17(2): 471-477(in Chinese) [5] 尹平河, 梁凤颜, 赵玲. TiO2/EP光催化降解水体中微污染磺胺嘧啶的研究. 环境工程学报,2010, 4(8): 1704-1708 Yin Pinghe, Liang Fengyan, Zhao Ling. Photocatalytic degradation of trace sulfadiazine in aqueous solution by TiO2 immobilized on expanded perlite. Chinese Journal of Environmental Engineering,2010, 4(8): 1704-1708(in Chinese) [6] 张从良, 王岩, 王福安. 磺胺嘧啶在水中的微生物降解研究. 生态环境, 2007, 16(6): 1679-1682 Zhang Chongliang, Wang Yan, Wang Fuan. Microbial degradation of sulfadiazine in water. Ecology and Environment, 2007, 16(6): 1679-1682(in Chinese) [7] Esplugas S., Bila D.M., Krause L. G.,et al. Ozonation andadvanced oxidation technologies to remove endocrine disrupting chemicals (EDCs) and pharmaceuticals and personal care products (PPCPs) in water effluents. Hazardous Materials, 2007, 149(3): 631-642 [8] Kehata K., NaghashkarN. J., El-Din M.G. Degradationof aqueous pharmaceuticals by ozonation and advanced oxidation processes: A review. Ozone Science Engineering, 2006, 28(6): 353-414 [9] Virender K., Sharma., Santosh K.,et al. Oxidation of sulfonamide antimicrobials by Ferrate(VI) . Environmental Science and Technology, 2006, 40 (23): 7222-7227 [10] Virender K., Sharma. Oxidative transformations of environmental pharmaceuticals by Cl2, ClO2, O3 and Fe(VI):Kinetics assessment. Chemosphere, 2008, 73(9): 1379-1386 [11] 梁凤颜, 尹平河, 赵玲, 等.水体中微污染磺胺嘧啶光催化降解行为. 生态环境学报, 2009, 18(4): 1227-1230 Liang Fengyan, Yin Pinghe, Zhao ling, et al. Photocatalytic degradation of trace sulfadiazine in water. Ecology and Environmental Sciences, 2009,18(4): 1227-1230(in Chinese) [12] 张凌, 楚红英, 常志显, 等. 超声波光催化协同降解对甲基苯磺酸水溶液的机理研究. 环境工程学报,2011, 5(4): 819-824 Zhang Ling, Chu Hongying, Chang Zhixian, et al. Study on mechanism of degradation 4-toluene sulfonic acid by sonophotocatalysis. Chinese Journal of Environmental Engineering,2011, 5(4): 819-824(in Chinese) [13] 张萍, 季彩宏, 韩萍芳, 等. 超声协同TiO2光催化降解4,4’-二溴联苯. 环境工程学报,2010, 4(8): 1823-1827 Zhang Ping, Ji Caihong, Han Pingfang, et al. TiO2 sonophotocatalytical synergistic degradation of 4,4’-dibromobiphenyl. Chinese Journal of Environmental Engineering,2010,4(8): 1823-1827(in Chinese) [14] 郭照冰, 郑正, 胡文勇, 等. 2,4-二硝基酚的超声波及协同降解研究. 环境科学学报, 2004, 24(2): 237-241 Guo Zhaobing, Zheng Zheng, Hu Wenyong, et al. Study on degradation of 2,4-Dinitrophenol by ultrasonic-wave and synergic system. Acta Scientiae Circumstantiae, 2004, 24(2): 237-241(in Chinese) [15] Zhaobing Guo, Ruo Feng. Ultrasonic irradiation-induced degradation of low-concentration bisphenol A in aqueous solution. Journal of Hazardous Materials, 2009, 163(2): 855-860 [16] 黄昱, 李小明, 杨麒, 等. 高级氧化技术在抗生素废水处理中的应用. 工业水处理, 2006, 26(8): 13-17 Huang Yu, Li Xiaoming, Yang Qi, et al. Application of advanced oxidation processes to antibiotic wastewater treatment. Industrial Water Treatment, 2006, 26(8): 13-17(in Chinese) [17] 魏瑞霞, 陈菊香. 超声技术处理难降解有机物的影响因素. 环境科技, 2009, 22(1): 64-66 Wei Ruixia, Chen Juxiang. Advance of application and research of ultrasonic technique in coke plant wastewater treatment. Environment Science and Technology, 2009, 22(1): 64-66(in Chinese) [18] Frisch M.J., Trucks G.W., Schlegel H.B., et al., Gaussian 03, Revision B.04. Pittsburgh PA: Gaussian Inc., 2003 [19] Ahmed A. Basfar, Hasan M. Khan, Ahmed A. Al-Shahrani, et al. Trihalomethane treatment using gamma irradiation: Kinetic modeling ofsingle solute and mixtures. Radiation Physics and Chemistry, 2005, 72(5): 555-563 -
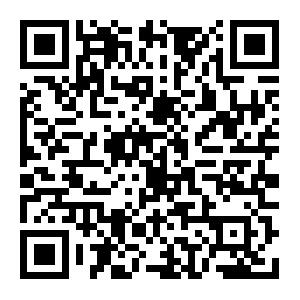
计量
- 文章访问数: 2420
- HTML全文浏览数: 1342
- PDF下载数: 1724
- 施引文献: 0