T型氧化沟提高脱氮效率的技术改造
Technical modification of denitrification enhancement in T type oxidation ditches
-
摘要: 采用延长边沟闷曝时间的方法对BOD降解模式T型氧化沟进行提高脱氮效率的改造。结果表明,边沟闷曝时间由0.5 h增至1 h,系统反硝化和硝化运行时间比tDN/tN由0.56调整至0.50时,提高了系统的NH3-N的硝化效率,强化了脱氮能力。工艺改造后出水NH3-N浓度由改造前15.5 mg/L显著降低至10.4 mg/L,达到了广东省地方标准(DB 44/26-2001)第一时段的二级排放要求;系统脱氮效率由改造前52.1%显著提高到68.3%,有效地解决了污水厂出水NH3-N浓度过高的问题;具有投资少、效果明显的特点,有一定的推广价值。Abstract: Though prolonging aeration time in side ditches, the technical modification of T type oxidation ditches of BOD biodegraded mode in the aspect of denitrification enhancement was constructed. Results proved that, when aeration time in side ditches was increased from 0.5 h to 1 h and radio of denitrification time to nitrification time, tDN/tN ,was changed from 0.56 to 0.50, percentage of nitrification was increased and ability of denitrification of the system was improved. After modification, concentration of NH3-N of outlet, 10.4 mg/L, dramatically lower than before, 15.5 mg/L, met discharged standards of Guangdong Province (DB 44/26-2001), and denitrification efficiency was dramatically enhanced from 52.1% to 68.3%. The problem of high concentration of NH3-N of outlet in wastewater plants was solved. With low investment and high efficiencies, the modification has certain of value of popularization and application.
-
Key words:
- T type oxidation ditches /
- denitrification /
- modification /
- aeration time
-
餐厨垃圾有机组分质量分数较高,利用其进行厌氧消化可以产生甲烷气体,产生的沼渣沼液经处理后也可用作有机肥料[1]。相比于湿式厌氧消化,干式厌氧消化处理的有机固废的固体(Total solid,TS)质量分数较高,一般可达15%~40%,其具有沼液产量少,单位容积产气率高、预处理成本低等优点[2]。物料的流变特性对厌氧消化的运行及性能有重要影响,同时,流变特性对水力过程如混合、泵送、脱水及干燥等过程均有较大影响[3-4]。如粘度高、流动性差的物料在厌氧消化过程中容易在反应器中形成滞留区,不利于有机质与微生物的相互作用,并会影响厌氧消化过程中的传质传热过程,进而影响有机质向甲烷的转化效率。因此,物料流变特性及其演变规律不光是厌氧消化过程中重要的设计参数,也是反应器优化运行的重要控制因子[5-6]。MIRYAHYAEI等[7]研究了污泥厌氧消化过程中流变特性与甲烷产气量及污泥脱水性能的对应关系。结果表明,污泥粘度越低,其消化过程中的产气量及挥发性固体(Volatile solids,VS)去除率越高。LIU等[8]研究了微波辅助H2O2预处理对污泥厌氧消化流变特性的影响。结果表明,该预处理技术可降低污泥的粘度,提高其流动性,并且也可降低其触变性,进而有助于提高VS去除率和甲烷产气量。以上等研究结果均表明,有机固体废弃物厌氧消化后,消化系统混合液的流变特性会发生变化,流动性相对于未消化之前会有所提高,但是对于混合液在厌氧消化过程中的流变特性变化则缺乏关注。此外,部分类型干式厌氧反应器(如Kompogas)采用了卧式推流、间歇进料的方式,随着污泥厌氧消化的进行,流变特性发生转变,直接关系到反应器不同运行时间、不同搅拌区域的混合特性。因此,明确不同组分物料在厌氧消化过程中的流变特性演变规律及其成因对提高厌氧消化效率、优化反应器运行至关重要。
厌氧消化反应器内混合效果主要受到局部流场的影响,通过计算流体力学(Computational fluid dynamics,CFD)模拟反应器内流场分布对混合过程的设计和优化十分必要[9-10]。曹秀芹等[11]借助实验和CFD模拟方法对污泥厌氧消化的混合效果及能耗进行实验和模拟,研究得出,针对含水率95%的污泥的最佳搅拌转速为180 r∙min−1。WU的研究[12-13]综合考虑了反应器形状,搅拌桨类型和安装位置等因素对混合效果的影响,这为反应器设计与运行的优化提供了参考。但目前厌氧消化反应器中的流场模拟主要集中于湿式厌氧消化过程,缺乏针对干式厌氧过程流场模拟及不同组分物料在厌氧消化过程中的流场演变规律探究。
本研究采用实际餐厨垃圾物料,通过改变其多糖,蛋白质及脂质的质量分数,研究不同有机组成物料厌氧消化过程中的流变特性变化及产甲烷特性,进而明确不同有机组成物料的产气特性差异,及各有机组成物料的表观粘度变化趋势,以探讨不同组成物料的产气量与其粘度的关联性。同时,以CFD模拟探究卧式反应器流场随物料流变特征变化的演变过程,以期优化不同组分物料在厌氧消化过程中的搅拌策略,为优化干式厌氧消化反应器的运行提供理论支撑。
1. 材料与方法
1.1 实验原料
接种污泥取自北京某污水处理厂中温厌氧消化罐(37~42 ℃,停留时间为18 d)的消化污泥,经过3 500 r∙min−1离心10 min后,弃去上层污泥,取底部高含固污泥并常温密封保存。餐厨垃圾取自食堂,人工分拣出样品中的塑料、纸屑、骨头、木头等杂质,用粉碎机将垃圾多次粉碎成匀浆,4 ℃保存备用。以馒头改变物料的多糖,蛋白质及脂质的质量分数。各物料的基本特征如表1所示。
表 1 底物及接种污泥质量分数Table 1. Mass fraction of substrates and inoculum sludge% 供试原料 TS VS 蛋白质 多糖 脂质 餐厨垃圾 25.3 23.6 28.1 37.7 25.4 馒头 61.1 60.6 12.4 77.6 3.1 接种污泥 15.3 5.4 8.1 4.2 5.4 注:蛋白质、多糖和脂质的质量分数基于TS。 1.2 实验装置及方法
厌氧消化实验采取产甲烷潜势测试(BMP)装置瑞典Bioprocess Control公司制造的全自动甲烷测试系统AMPTS II。反应器为600 mL玻璃瓶,有效容积为400 mL。向反应瓶依次加入接种污泥及反应底物后,立即拧紧橡胶塞,并向反应瓶内充5分钟N2以排空瓶内的氧气,保证厌氧环境。密封后的玻璃瓶放入恒温水浴锅((37±1) ℃)中温厌氧消化。产生的沼气经过3 mol∙L−1的NaOH溶液去除CO2等酸性气体,剩余气体经过检测器自动计量并计为甲烷体积。
接种污泥与反应底物的接种比(基于VS)为2。实验前所有物料均稀释到与接种污泥相同的TS质量分数,以排除TS质量分数对物料流变特性的影响。以往研究表明餐厨垃圾中碳水化合物(多糖)的质量分数基本为30%~70%(基于干重),而蛋白质的质量分数为10%~30%,脂质质量分数为10%~30%[14-15]。以此数值为参考标准并以多糖质量分数作为调控对象,通过向实际餐厨垃圾中投加馒头将其多糖质量分数(基于干重)分别调至50%(Car50%),60%(Car60%)和70%(Car70%),对照组(Control)不投加馒头,多糖质量分数为37.7%。每种组分比例物料均设置3组平行实验。
1.3 分析方法
污泥及各原料的的TS、VS质量分数采用重量法[16]测定。厌氧过程中的污泥样品经8 000 r·min−1离心10 min后取上清液过膜(0.45 μm;Savillex)后,用于测定溶解性指标。溶解性多糖和溶解性蛋白质的测定分别采用Dubious分光光度法[17]和修正的Lowry法[18]。固体样品中的多糖、蛋白质及脂质质量分数测定参考文献[19]。厌氧消化过程中的污泥样品粘度采用ConTec-Viscometer5型流变仪(Spindle L3C型转子,Fungilab,西班牙)测定,每个样品先在250 r·min−1的转速下预剪切30 s,之后再在2 min内剪切速率从0 r·min−1升至250 r·min−1测定样品粘度变化。样品的剪切应力与剪切速率采用Herschel-Bulkley方程拟合(公式1)[20]。
τ=τ0+K⋅γn (1) 式中:τ为剪切应力,Pa;τ0为屈服应力,Pa;K为稠度系数,Pa·sn;γ为剪切速率,s−1;n为流动指数,无量纲。
1.4 CFD模拟方法
为了定量化分析厌氧消化过程物料的流变特征差异及其演变过程对反应器内流场的影响,针对某实际干式厌氧消化中试反应器,开展了相应的流场模拟研究。以某食堂的餐厨垃圾为厌氧消化物料,通过投加外源馒头改变物料的多糖,蛋白质及脂质质量分数,进而研究不同组成物料厌氧消化过程中的流变特性变化,并以此为数据基础探究不同组分物料在该实际中试厌氧消化反应器中的流场变化。该卧式搅拌干式厌氧发酵反应器长度6 m、高度2.8 m、回转直径2.2 m,容积约为20 m3。搅拌桨轴心与回转圆心重合,搅拌桨采用交错方式分布于搅拌轴上,每450 mm距离分布一个桨叶,相邻桨叶间夹角90°,每4个桨叶为一组,共有三组12个桨叶。桨叶为改良的T型搅拌桨,桨叶末端为勺型。进料端第一组桨叶间隔设置4个扰流杆,杆与桨夹角45°。
反应器几何结构及网格划分如图1所示。CFD模拟平台为ANSYS Fluent 2020 R2软件,具体计算方法如下:1) 模型:模拟采用单相流模型,湍流模型为SST k-ω模型;2) 材料:反应器中的流体材料为厌氧消化过程中的实际物料,其非牛顿流体粘度通过UDF文件赋予,密度近似于水的密度;3) 域条件:分为流体域和旋转域,稳态计算时,旋转域的旋转采用旋转坐标系方式;瞬态计算时,旋转域采用滑动网格方式进行旋转;4) 边界条件:旋转域和流体域的交接面采用interface方式进行耦合,其余各壁面包括搅拌轴,进出口,顶盖,底面均设置为静态壁面,暂不考虑进出物料,只考察物料混合过程中的流场分布;5) 计算方式:采用稳态求解,搅拌桨转速设置为5 r·min−1,迭代步长为1 000步。
2. 结果与讨论
2.1 不同有机组成物料厌氧消化过程中的流变及产甲烷特性
不同有机组成物料厌氧消化过程中的粘度变化趋势如图2所示。由图可知,随着剪切速率的升高,各物料的表观粘度不断降低,表明物料为假塑型非牛顿流体[8]。由图2(a)~图2(d)可知,随着厌氧消化的进行,不同有机组分物料的粘度总体均呈现不断下降趋势,表明随着厌氧消化的进行,物料非牛顿特性减弱,流动性变强[21]。值得注意的是,car50%和car70%的实验组前期粘度下降较快,在第10天之后粘度基本达到最小值,后期随着厌氧消化的进行粘度变化趋势不再明显。而对照组和car60%的实验组粘度下降趋势则较慢,在第5天之后粘度才有明显下降,且这种下降趋势一直维持到第35天。这与不同组成物料的产气速率情况基本一致(表2),即car50%和car70%实验组产气高峰相对靠前,而对照组和car60%实验组产气高峰比较靠后。此结果表明物料的流变特性与其厌氧消化产甲烷特性有直接关系,物料粘度下降有利于产甲烷速率的提高。
表 2 不同有机组成物料产甲烷特性Table 2. Methane production characteristics of substrates with different organic compositions实验组 累积甲烷产量/(mL·g−1) 最大产甲烷速率的时间/d 最大产甲烷速率/(mL·(g·d)−1) Control 391.1 ± 26.5 22 41.7 ± 5.6 Car50% 427.5 ± 37.4 15 34.3 ± 5.1 Car60% 373.8 ± 12.6 26 35.3 ± 3.6 Car70% 488.7 ± 28.7 15 40.4 ± 6.9 图2(e)~图2(f)进一步对比了厌氧消化过程中物料不同组分比例下的粘度差异,结果表明,car50%和car70%实验组的表观粘度低于对照组和car60%实验组,这与各组物料的累积产甲烷量相对应(表2)。但随着厌氧消化的进行,有机物不断释放,到第35天各组物料的表观粘度差异不再明显。MIRYAHYAEI等[7]的研究结果也表明污泥粘度越低,其消化过程中的产气量及VS去除率越高,这主要由于流动性的提高可促进微生物与有机质的传质过程,进而提高产气量;而基质流动性较差时则可能在反应器内形成停滞区,造成污泥聚集,不利于微生物对有机质的利用。
各组物料厌氧消化过程中的屈服应力τ0,稠度系数K及流动指数n的变化如表3所示。由表3可知,随着厌氧消化的进行不同组分物料的屈服应力τ0和稠度系数K均总体呈现不断下降趋势,表明随着反应的进行物料的假塑性减弱,流动性变好,但流动指数n的变化波动较大,不具有明显升高趋势。同时,对照组及Car60%物料的屈服应力τ0普遍较另外两组更大,这与其表观粘度结果一致,但各组物料消化过程中的稠度系数K及流动指数n差异并不明显。
表 3 不同组分物料厌氧消化过程中的流变参数变化Table 3. Change of rheological parameters during anaerobic digestion实验组 τ0/Pa K/(Pa·sn) n R2 Control-day0 5.019 4 2.582 1 0.400 0 0.993 6 Control-day5 4.292 1 3.387 3 0.345 0 0.978 3 Control-day10 5.288 7 0.950 6 0.533 3 0.992 7 Control-day20 2.439 8 0.901 5 0.485 0 0.994 5 Control-day35 1.016 6 0.810 4 0.462 5 0.981 5 Car50%-day0 4.741 6 2.474 5 0.432 2 0.991 0 Car50%-day5 4.297 8 1.603 7 0.460 0 0.996 2 Car50%-day10 1.488 1 1.628 6 0.382 2 0.984 5 Car50%-day20 0.779 0 1.553 5 0.377 7 0.989 2 Car50%-day35 0.593 7 1.522 9 0.348 6 0.995 2 Car60%-day0 6.647 1 1.913 0 0.479 2 0.990 2 Car60%-day5 2.369 0 5.234 7 0.257 1 0.991 8 Car60%-day10 2.916 1 1.255 7 0.460 9 0.990 3 Car60%-day20 2.329 2 0.957 6 0.486 8 0.991 0 Car60%-day35 1.497 0 0.906 1 0.442 7 0.993 1 Car70%-day0 2.994 3 3.954 5 0.356 8 0.994 6 Car70%-day5 1.362 6 2.914 2 0.340 4 0.994 1 Car70%-day10 2.525 8 0.987 4 0.468 7 0.992 6 Car70%-day20 1.149 2 1.472 4 0.397 5 0.993 8 Car70%-day35 1.212 8 1.557 6 0.396 0 0.994 7 2.2 厌氧消化过程物料流变特征与有机物转化的关系
物料不同有机组分比例下厌氧消化过程中的TS、VS质量分数变化及所释放的溶解性蛋白质、多糖浓度变化如图3所示。由图3(a)及图3(b)可知,各组物料初始TS、VS质量分数基本一致,但对照组和car60%实验组的TS、VS质量分数下降较慢,至第35天TS分别下降了14.2%和11.7%,VS分别下降了32.1%和29.1%,而car50%和car70%实验组的TS、VS质量分数则下降得较快,至第35天TS分别下降了24.8%和25.7%,VS分别下降了36.9%和36.2%。这与各组实验的粘度差异及产甲烷特性结果一致,表明TS、VS下降越快,有机物降解、释放越快,粘度降低越明显,有利于产甲烷效率的提高。TS质量分数是影响污泥流变特性的重要因素。LIU等[22]的研究结果表明TS质量分数的升高可降低颗粒之间的距离,加强颗粒之间的相互作用;同时TS质量分数越高,流动特性指数n越低,稠度系数K越高,表明其假塑性越强,颗粒之间的相互作用得到加强。WANG等[23]的研究也表明厌氧消化过程中的甲烷产量会随着物料TS质量分数的升高而降低。由图3(c)可知,随着初始物料多糖质量分数的升高,相应的蛋白质质量分数自然降低,消化过程中溶解性蛋白质的释放量也随之降低。同时,各组物料所释放的溶解性蛋白质均随着厌氧消化的进行而不断升高,也表明污泥絮体不断溶解,有利于其屈服应力和表观粘度的降低[24]。但各组物料溶解性多糖的释放差异并不明显(图3(d))。
将各组物料厌氧消化过程中的TS、VS质量分数及各流变参数的变化汇总如图4所示。由图可知,物料TS、VS质量分数与其屈服应力τ0具有一定的线性相关关系,进一步证明TS、VS质量分数的降低有利于降低物料屈服应力,提高其流动性。但物料TS、VS质量分数与其稠度系数K及流动指数n的相关关系并不明显。因此,TS、VS质量分数可作为定量预测物料屈服应力的良好指标,并可在一定程度上预测物料的流变特性。
2.3 反应器内流场随厌氧消化过程流变特征的演变
通过CFD流场模拟,不同有机组成物料厌氧消化过程中的反应器流场速度梯度分布如图5所示,死区(速度梯度小于0.02 m·s−1的区域)率变化如图6所示。
由图5可知随着反应的进行各物料搅拌过程中的速度梯度均呈现不断升高的趋势,表明随着反应的进行物料粘度降低,反应器内流场逐渐变好。由图6(a)可知,随着厌氧消化的进行,反应器内死区率不断降低,且Car50%和Car70%物料在消化过程中的死区率普遍较另外两组更低,这与各组物料的表观粘度及产甲烷特性结果一致,表明流动性的提高有利于物料在反应器内的有效混合,进而提高物料的产甲烷效率。Car70%物料由于其多糖质量分数最高,前期水解速率较快,在第0~5天死区率降低明显,其他各组物料均在第5~10天死区率降低最为明显,表明不同物料由于其组分及流变特性的不同,死区率演变特点也各不相同。同时,由图6(b)~图6(d)可知,各组物料搅拌过程中的死区率均与其TS质量分数、屈服应力τ0及表观粘度(剪切速率为15 s−1)呈一定的正相关关系,也表明随着反应的进行,有机物不断释放,物料TS不断降低,屈服应力及表观粘度不断降低,流动特性变好,从而使反应器内混合效果变好,死区率不断降低。因此,结合反应器流场模拟结果,可考虑在厌氧消化后期降低搅拌转速或减少搅拌时间,从而在不降低搅拌效率的同时节省搅拌能耗。MAO等[25]研究了食物残渣和鸡粪共消化过程中搅拌模式和时长对甲烷产气量的影响。其CFD模拟结果表明高TS和高粘度会减弱叶轮的传送过程,使得反应器内湍流度较低,降低物料混合效果。同时,CFD模拟结果表明当间歇搅拌时间能够使基质足够均匀时,增加搅拌时间或改为连续搅拌无助于产气量的提高。因此,基于厌氧消化反应器的流场模拟可为搅拌策略的优化提供重要理论基础,从而减少实际工程的放大投资。
3. 结论
1) 不同有机组成物料厌氧消化过程中的流变特性与其产甲烷效率具有重要关系,物料粘度越低,流动性越好,其甲烷产气量越高。
2) 物料流变特性的差异主要来源于TS、VS质量分数以及溶解性有机物释放的差异,物料TS、VS质量分数越高,其表观粘度越高,流动性越差,同时物料的屈服应力与其TS、VS质量分数具有一定的线性相关关系。
3) 随着厌氧消化的进行,物料粘度不断降低,反应器内流场逐渐变好,死区率降低,且死区率与物料TS质量分数、屈服应力及表观粘度具有正相关关系。
-
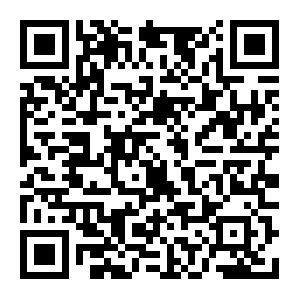
计量
- 文章访问数: 2915
- HTML全文浏览数: 1858
- PDF下载数: 791
- 施引文献: 0