吡啶类离子液体对青海弧菌Q67的混合毒性评估
Evaluation on the Combined Toxicity of Pyridium-Based Ionic Liquids to Vibrio Qinghaiensis sp. -Q67
-
摘要: 混合污染物产生的累积与毒性相互作用具有潜在的环境与健康风险。以6种吡啶类离子液体(IL):丁基溴化吡啶([Bpy]Br)、己基溴化吡啶([Hpy]Br)、辛基溴化吡啶([Opy]Br)、丁基氯化吡啶([Bpy]Cl)、己基氯化吡啶([Opy]Cl)和辛基氯化吡啶([Opy]Cl)为混合物组分,应用直接均分射线法(EquRay)和均匀设计射线法(UD-Ray)分别设计4组二元IL混合物和2组三元混合物,每组混合物包括5条具有不同浓度配比的混合物射线。应用微板毒性分析法测定6种IL及其30条混合物射线对青海弧菌Q67的发光抑制毒性,以浓度加和(CA)为加和参考模型分析混合物毒性相互作用。结果表明,Logit函数能有效地拟合6种吡啶IL及其30条混合物射线的浓度-效应数据。若以半数效应浓度的负对数(pEC50)为毒性指标,6个吡啶IL对Q67的毒性与烷基链上碳原子数目正相关,且每增加2个碳原子,其毒性约增加1。IL的阴离子(Br-或Cl-)对毒性没有影响。除己基氯化吡啶([Hpy]Cl)和辛基氯化吡啶([Opy]Cl)的二元混合物呈现明显拮抗作用外,其他二元及三元混合物都为加和作用。Abstract: The cumulative toxicity and toxicity interaction of mixtures have potential hazards and risks to the environment and human health. Selecting six pyridium-based ionic liquids (ILs), 1-butyl pyridinium bromide, 1-hexyl pyridinium bromide, 1-octyl pyridinium bromide, 1-butyl pyridinium chloride, 1-hexyl pyridinium chloride, and 1-octyl pyridinium chloride as mixture components, we employed the direct equipartition ray design and uniform design ray methods to design four groups of binary mixtures and two groups of ternary ones, respectively. Every group of mixture contains five mixture rays with different concentration ratios. The toxicities of the six single ILs and 30 binary and ternary mixture rays to Vibrio qinghaiensis sp.-Q67 (Q67) were determined by using the microplate toxicity analysis, and the mixture toxicity interaction was identified by selecting the concentration addition (CA) as an additive reference model. It was shown that concentration -response curves (CRCs) of six ILs as well as 30 binary and ternary mixture rays can be effectively described by the Logit function. Selecting the negative logarithm of median effective concentration (pEC50) as a toxicity index, the toxicity of six ILs to Q67 has a positive relationship with the length of alkyl chain in IL. Every two-carbon augment on the alkyl chain almost makes the toxicity (pEC50) of IL increasing one. The anion, Br-or Cldoes not affect the toxicity of ILs on Q67. Except that the group of binary mixtures between 1-hexyl pyridinium chloride and 1-octyl pyridinium chlorides produces significant antagonism, the other five groups of binary and ternary mixtures display the concentration additive action.
-
油气井采出液通常是原油、天然气、水、砂和其它杂质组成的混合液,油、气、水、砂混合液的多相分离贯穿油气行业开采、炼制、使用全过程,是最重要的工艺单元之一。我国绝大多数陆上油田进入开采中后期时,采出液成分更复杂、分离难度更大。我国海洋石油开采受海洋环境、工作条件的局限,往往需要更高效、稳定的多相分离技术,从而满足海洋油气平台中采出液处理量大、分离指标高、空间受限等问题。目前,工程中普遍采用静态重力沉降分离技术,油、气、水、砂混合液在重力沉降罐中利用重力分离作用实现各相分离,且混合液停留时间越长,效果越好。但是,随着油气产量增加、含水率升高,沉降停留时间降低,许多老旧油田面临污水处理能力不足、难以达标等难题。同时,重力沉降罐存在罐体重、占地大、成本高、耐压性差、效率低等问题,从而使其在陆上新油田和海上油田上的应用受到限制[1-2]。随着采出液处理、排放和回注等相关的环保标准日益提高,开发高效、经济、稳定的油气井采出液处理技术和装备,对于我国油气行业长期可持续发展具有重要意义。
为突破传统油田以大型沉降罐为主的重力沉降分离方法,本课题组深入研究油气水多相流动机理,提出管道分离概念,并以此为基础开展油、气、水、砂混合液多相动态分离为主的技术和装备创新,开发了以螺旋管、T型管、旋流管、气浮管、聚结管等为核心的系列管道分离技术和成套装备,并通过技术示范和推广应用,获得了很好的经济效益、环境效益和行业影响力[3-7]。本文阐明了管道分离技术的原理及各类管道设备的分离性能,并通过分析课题组已成功实施的典型应用案例介绍了该技术的实际应用情况,为油气田开发中的水油、水泥等非均相分离提供参考。
1. 管道分离技术原理、设备与多相分离性能
1.1 螺旋管分离的技术原理及数值模拟
螺旋管形状如图1(a)所示,类似于直立的弹簧,混相介质入口在底部,顶部为轻质相出口。螺旋管分离原理是两相混合液在螺旋管内流动过程中受离心力和重力作用,密度较大的重质相移向螺旋管外侧,密度较小的轻质相移向螺旋管内侧,图1(b)表示为管道横截面上的油水两相分布;流动状态稳定后,重质相从螺旋管外侧壁面小孔流出,轻质相由螺旋管顶部出口流出,从而实现两相分离[8-9]。油水分离效果主要由ρw/ρo(ρw为水相密度,ρo为油相密度)和u2/(Rg) (u为流体速度,R为螺旋半径,g为重力加速度)两个无量纲量决定。稠油ρw/ρo约为1,分离效果主要取决于u2/(Rg)大小。图1(c)是螺旋管油水分离实验照片,周边喷出的粉红色液体是经过染色的水,油从顶部连接的管道排出。
设计管径40 mm、旋转半径400 mm、螺距100 mm、入口位于下端的螺旋管模型,对油水两相在螺旋管内的流动情况进行数值模拟。图2为入口流速1.0 m·s−1、含油率0.305时第1圈和第5圈管路末端截面油相分布情况(红色表示油相,蓝色表示水相)。可以看出,在重力和离心力作用下,水相位于管截面侧下方,油相则集中于管路侧上方。因此,在螺旋管外壁面下方适当位置处开设出流孔,可有效导引出管路内水相,从而达到油水两相分离目的[10]。
1.2 梯型管(T型管)分离技术原理及数值模拟
T型管主要利用重力、浮力和分层滑移等作用实现气-液、液-液预分离,一般由2到3根水平管和多根垂直管组成,具有1个入口和2个出口(见图3(a))。油水或气液两相混合液在水平管流动过程中,重质相受重力作用通过T型分岔结构与垂直管道下降到底部水平管汇聚,密度较小的轻质相在浮力作用下通过T型结构与垂直管上浮到顶部水平管,形成两相的分层流。T型分岔结构的功能在于实现两相流动路径选择,垂直管是两相动态交换流动的通道,而水平管则发挥输送、聚集等功能[11-15]。图3(b)为T型管油水分离中试装置。
T型管分离效果取决于T型分岔结构设计、水平管和垂直管管径、垂直管高度与数量、上下水平管的分流比等参数,且可根据不同多相分离需求设计不同T型管结构形式。例如,气液相分离T型管顶部水平管、垂直管可改为倾斜方式以减少出口处的扰动,进、出口可增加整流、导流装置等。图4为油密度为900 kg·m−3、入口含油率为15%时3层T型管内油相体积相含率等值线分布色图(红色表示油,蓝色表示水相),模拟结果证实,T型管对于油水两相具有优异的分离性能。
1.3 旋流管分离技术原理及数值模拟
旋流管分离利用非均相介质密度差,通过旋转流场不同离心力产生的运动路径实现不同介质的高效分离。根据起旋方式、进出口结构的不同,旋流管分离器可分为柱型旋流分离器、导流片型旋流分离器[16-18]。
柱型旋流器通过水平入口的切向起旋,油水两相在柱形分离段内高速旋转流动,各相介质在密度差作用下产生不同离心力,如图5(a)所示,重质相(如水或砂)在重力和离心力作用下向管壁聚集并螺旋向下运动,最终从底部出口排出;轻质相(如油或气)在旋流器中心聚集,与重质相轴向运动方向相反,最终从顶部出口排出。导流片型旋流器通过流体的轴向起旋,轻质相向轴心聚集形成油核或气核,通过轴向的出口引出;重质相甩向管道边壁,通过边壁处的接口管段引出。与柱型旋流器相比,导流片型旋流器内部流场对称稳定,没有轴向的反向流动;可水平、垂直或倾斜安装或缩小径向尺寸,在井下或尺寸受限的场景具有很好的优势。
柱型旋流器油水分离实验(图5(b))结果显示,通过控制油、水掺混比例,进入旋流器的油水可在离心力作用下形成油核;控制顶部轻质相出口和底部重质相出口的阀门调节分流比(顶部出口流量与入口流量的比值),随着分流比α由0增加到0.95,油核可形成粗细和长短不同的形状[19]。
进一步采用数值模拟的方法研究油水分离过程与效果(图6,红色表示油相,蓝色表示水相),其中模型设置条件为:管道直径75 mm,导流片与管道轴向夹角20°,入口流量10 m3·h−1,入口含油率为10%,油品粘度245 mPa·s,油出口流量为总入口流量30%,油相密度由850 kg·m−3增加至980 kg·m−3。可以看出,随着油相密度增大,出水口含油率逐渐升高,形成的油核中油相含率逐渐降低;密度接近的油水两相分离更为困难[20]。
1.4 其他管道分离技术
基于上述管道分离技术,并融合其他分离技术,发展出多种复合分离新技术和新装置。
1)旋流气浮分离。气浮除油采用加压溶气装置向污水中溶入气体,释放产生大量微小气泡,气泡黏附细小油粒、悬浮物等形成絮状物,进一步通过浮力作用实现分离。旋流气浮分离有效利用气浮与低强度旋流离心场的协同作用,大幅增加气泡与油滴碰撞聚并机率,减少停留时间加快上浮分离速度,从而提高分离效率。气浮技术也可以与T型管等结合形成管道气浮装置[21]。
2)管式整流-聚结。为提高分离效果,可在管道适当部位增大管段直径,加设平行多孔板降低雷诺数,促进流态稳定。此外,还可以在适当管段安装波纹填料,延长油水通过路径,增大油滴碰撞、粘附、聚并概率,提高油水分离效果[22]。
3)电场旋流聚结器。在旋流管内安装带孔平板或筒状电极,从而在旋流场内赋予电场力,通过强化电泳聚结、偶极聚结、震荡聚结等作用显著改善严重乳化状态下油水分离效果。此外,旋流管中还可与电磁破乳、超声波破乳等技术融合,强化处理乳化油,提高油水分离效率[23]。
4)管道除砂洗砂器。油气开采过程中,不可避免地会把地下的泥砂带到地面。开采中后期,由于长期持续压裂和吞吐采油采气,出砂越来越严重,对管线及沿程设备造成危害,且减少沉降罐有效容积、降低换热效果。可将管道除砂洗砂器安装在管线上排砂或在罐底铺设管网定期排砂,再通过旋流分离器液固分离。分出的含油泥砂还可通过管式旋流分离器的剪切洗涤作用进一步降低其含油率,减少外排污染[24]。
2. 管道分离技术典型应用案例
近年来,笔者团队将管道分离技术在我国陆上油田和海上油田开展了大规模示范应用[25-26]。相应的螺旋管、T型管、旋流管等分离器可单独进行分离应用,亦可根据不同需求进行模块化组合应用。
2.1 T型管分离器在某油田联合站四相混合液分离工程中的应用
某油田联合站进站混合液情况为流量2 000 m3·d−1,含油率55%、气液比10:1、含泥砂。工程目标为对混合来液进行油、气、水、砂分离,去除携带的泥沙。本工程首先用一组T型管进行气、液分离,之后对除气后的液体进行旋流分离去除泥沙。除砂后油、水混合液进入第二组T型管进行油、水分离,油进入联合站油处理工艺线,含油污水经2级旋流分离,含油量低于150 mg·L−1后排入污水罐。该项目实现了油田采出液在管道输送过程中的动态分离[27],工艺流程如图8所示。
通过对原三相分离器内沉积的泥沙样品进行分析后发现,沉降泥沙粒径在30~120 μm的组分约占85%。以此泥砂粒径分布为依据,设计安装了管道式旋流除砂器(如图9(a)),分离出泥沙经干燥后见图9(b)。泥砂粒径分布检测结果见表1,分离出泥沙中粒径在44~64 μm范围的组分占比为47.96%,大于44 μm的组分占70%,与设计参考数据基本吻合。
表 1 旋流除砂器分出的泥砂粒径分布Table 1. Granularity distribution of sand removed by cyclone sand remover粒径/μm 质量占比/% 累计占比/% <44 0.026 2 0.026 2 44~64 0.479 6 0.505 8 64~91 0.015 5 0.521 3 91~101 0.087 1 0.608 4 101~125 0.073 8 0.682 2 125~150 0.088 8 0.771 0 150~178 0.016 8 0.787 8 178~420 0.036 6 0.824 4 >420 0.172 4 0.996 8 图9(a)中右侧罐体为该联合站三相重力沉降分离器,2用1备,单罐长度12 m、直径2.6 m,有效容积60 m3,净重12 t,湿重约52 t。总重量和尺寸规格远大于管道式多相分离装置。在罐体内油水静态分离时间约为45 min,而相应的管道分离装置采用动态分离方法,分离时间小于4 min。管道式四相分离装置解决了原有罐式三相分离器除砂的难题,并在保持油气水三相分离指标相同的情况下,分离效率(速度)提高了10倍。
2.2 柱形旋流分离器在某气田井口除砂工程中的应用
某气田井日产气量1 600 m3,产水24.7 m3,井口出砂影响下游生产管线和设备。设计安装了管道式高压井口除砂装置(见图10(a)),设计压力为25 MPa。该除砂装置针对气、固分离需求,将油田常用的锥体分离方案改为承压结构优良的柱形分离管段,同时增加内部构造以减少砂粒随气体排出,具有结构简单可靠、分离性能好、使用寿命长等优点。现场取样(图10(b))分析表明,小于400 μm小颗粒砂粒质量占比为87.2%,600 ~ 800 μm范围的球形砂粒质量占比为12.8%,图10(c)给出了该气井出砂粒径累计百分比,与用户提供的该生产区块地下出砂粒径数据吻合,通过半年连续运行监测,地面长输管道内积砂量较其它气井明显减少,表明气固旋流分离器设计合理、运行正常。
2.3 T型管与旋流管分离器结合处理某油田企业含油污泥
东北某油田技术服务公司采用两步法处理当地产生的含油污泥:第1步采用热洗、离心分离等技术手段将大于15%的含油率降至5%以下;第2步采用热解或其它方法降低含油率至2%以下。在含油率指标不变,检测对象由湿泥转变为干泥后,该公司自有的污泥处理工艺就很难达标,处理完的污泥含油率超出标准2~4倍。为降低改造成本、避免处理工艺复杂化,采用管道分离技术对该处理工艺进行局部改造。具体做法是在第1步的处理环节中,在原有的调质罐内增加T型管分离器、旋流管分离器,与原工艺一起加强除油功能,通过液固分离将大部分含油污水从处理流程中提前分流,减小对后续污泥处理的影响。工程应用结果表明,工艺改造后处理的含油污泥含油率降低50% ~ 60%,基本实现了预期5%以下的设计目标。
图11(a)是经局部改造后的污泥处理装置,T型管分离器、旋流管分离器与原有工艺流程融合,处理能力为30 m3·h。相对于改造前,技改后处理出来的泥团表观细腻、颜色浅、黏度低,干燥后泥团无黑芯(图11(b))。含油率检测结果表明,采用管道分离技术进行改造后,污泥含油率降低60%,数据对比见图12。管道分离技术提高了原工艺含油污泥处理效率和污油回收率,降低了处理成本,有利于实现油泥治理达标。
3. 结语
管道分离技术基于力学复合原理的物理分离方法,分离速度快、效率高,不投加化学药剂,无二次污染风险。工程应用实践表明,与传统重力沉降罐相比,运用管道分离技术的设备可减少40%以上占地和体积,运行重量降低50%以上,适合空间和承载力受限条件下的工程建设或改造。与传统分离技术和设备相比,管式分离器易与现有工艺融合衔接,布置灵活,移动方便。管道分离装置按其结构特征可归结为管道类设备进行日常操作和管理,可有效降低监管成本和运行中的风险,管道分离技术被国内石油生产企业逐渐接受并成为企业生产工艺改造升级、降本增效的一种技术手段[28]。
-
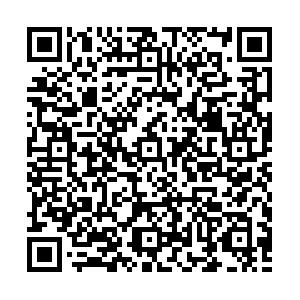
计量
- 文章访问数: 2092
- HTML全文浏览数: 2092
- PDF下载数: 27
- 施引文献: 0